The medical industry has stringent standards and a relentless pursuit of precision, presenting unique challenges to metal stamping. As medical devices become increasingly complex and demand continues to grow, understanding the nuances of metal stamping in this field becomes crucial. Here is an in-depth discussion of the key considerations that must be taken into account.
Precision is of Paramount Importance
In the intricate world of medical devices, precision is not just a luxury but a necessity. Every edge of a surgical blade, every joint of a robotic surgical arm, and every tiny component of a heart implant must be meticulously crafted according to exact specifications. The reasons are as follows:
Rigorous Tolerances: In industries such as automotive or consumer electronics, minor variations in parts may be acceptable. However, in medical devices, even the slightest deviation can have serious consequences. For instance, an imprecise component in a pacemaker could lead to device failure, endangering the patient's life. Therefore, the tolerances for metal stamping in medical devices are among the strictest in the manufacturing industry.
Necessity of Medical-Grade Metals: Not all metals are created equal. While a specific alloy may be perfectly suited for a car body or kitchen utensils, it could have disastrous consequences when implanted in the human body. Medical devices require metals with biocompatibility, meaning they do not cause adverse reactions with human tissue. Metals such as surgical stainless steel, titanium, and certain nickel and cobalt alloys are often preferred. These metals not only provide the required strength and durability but also ensure that the body does not reject the device.
Advertisement
Consistency is Key: Imagine a scenario where two batches of identical surgical instruments perform differently. Such inconsistency could be catastrophic in the medical field. Regardless of whether the manufacturer produces ten or ten thousand devices, each device must function identically to its counterpart. This level of consistency ensures that surgeons and medical professionals can accurately understand the expectations of the device, allowing them to focus on their primary goal: patient care.
Material Selection is Crucial
Delve into the field of medical devices, and we find that every choice made in the manufacturing process holds significant importance. Among these choices, selecting the right metal is a critical decision. Below is a detailed explanation of why material selection is so important:Corrosion Resistance: The human body is a complex environment, filled with various fluids ranging from blood to gastric juices. When medical devices (whether surgical tools or implants) are introduced into this environment, they must remain unaffected. Corrosion can compromise the integrity of the device, leading to malfunctions, or worse, releasing harmful substances into the body. Metals such as stainless steel and titanium are renowned for their excellent corrosion resistance and are typically the materials of choice for such applications.
Strength and Durability: Medical implants, such as hip replacements or stents, need to withstand the wear and tear of daily life. This is not just to survive the initial implantation but to ensure that their lifespan does not degrade. The material must be robust enough to withstand mechanical stress, whether it's the continuous beating of a heart valve or the load-bearing function of a spinal implant. Alloys that combine strength and flexibility, such as cobalt-chromium alloys, are often favored for these demanding applications.
Biocompatibility: Perhaps the most critical factor, biocompatibility ensures that the chosen metal does not harm the body. Some metals can trigger an immune response after implantation, leading to complications such as inflammation or device rejection. Metals that are inert or beneficial to the biological environment must be selected. For instance, titanium is not only strong and corrosion-resistant but also durable. It is also known for its excellent biocompatibility, often fusing seamlessly with surrounding bones and tissues.
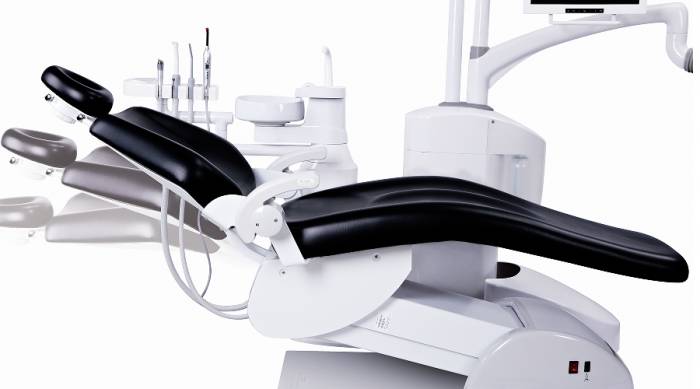
Sterilization and Cleaning
In the healthcare field, cleanliness is not just about appearance; it's about health. It's a matter of life and death. Medical devices, whether used externally or implanted, come into direct contact with patients. Any contamination can lead to infection, complications, or even fatal outcomes. This makes the sterilization process crucial. But how does metal stamping fit into this picture? Let's delve deeper:
Heat Resistance: One of the most common methods for sterilizing medical equipment is autoclaving, which involves placing the device in high-pressure steam at temperatures typically above 121°C (250°F). For metal stamping parts, this means they need to be made from materials that can withstand such high temperatures repeatedly without deformation, weakening, or any form of degradation. Metals such as stainless steel and certain titanium alloys are favored in this regard due to their ability to withstand high thermal stress.
Chemical Resistance: In addition to heat resistance, chemical disinfectants like ethylene oxide, hydrogen peroxide, and formaldehyde are also frequently used to sterilize medical devices. These chemicals are potent and corrosive. The metal stamping components of medical devices must be able to resist the corrosive nature of these chemicals. This resistance ensures that the device remains intact and functional even after multiple rounds of chemical sterilization. Moreover, chemical resistance ensures that no harmful residues that could harm patients remain on the device.
Smooth Surfaces: While not directly related to the performance of the metal, the stamping process must ensure that the parts have smooth surfaces, free of cracks or rough patches. These imperfections can harbor bacteria or other pathogens, thereby reducing the effectiveness of sterilization. Smooth surfaces not only aid in effective sterilization but also minimize the risk of tissue irritation or injury when using the device.Regulatory Compliance and Certification
Exploring the intricate regulations of the medical industry can be daunting. However, these regulations are in place for a reason: to ensure the utmost safety and efficacy of medical devices that millions of people rely on daily. When it comes to the stamping parts used in these devices, the stakes are even higher. This is why regulatory compliance and certification are non-negotiable:
Adherence to FDA Guidelines and International Standards: The U.S. Food and Drug Administration (FDA) has established strict guidelines for medical devices to ensure their safe use for humans. These guidelines cover everything from the materials used to manufacturing processes and final product testing. For stamping parts, this means they must be made from approved materials and undergo specific tests to verify their safety and performance. In addition to the FDA, international organizations like the International Organization for Standardization (ISO) have their own set of standards, such as ISO 13485, which is specifically for quality management systems in the medical device industry.
Stringent Testing and Quality Inspections: Medical devices undergo a series of tests before they are released to the market. For stamping parts, these tests may include tensile strength evaluations, corrosion resistance assessments, and biocompatibility tests. Each test ensures that the component can withstand the rigors of medical use without failure or causing harm. Regular quality inspections during the manufacturing process further ensure that each batch of components meets the set standards, minimizing the risk of defects.
Production in Certified Facilities: This involves not just the final product; it also pertains to the components that make up the final product. The location and manner in which these components are manufactured are crucial. Facilities that produce stamping parts for medical devices must be certified to ensure they adhere to specific cleanliness and quality standards. This may involve clean rooms, specialized ventilation systems, and strict protocols to prevent contamination. Regular audits and inspections help ensure that these facilities maintain the highest standards at all times.
Advanced Miniaturization Stamping Technology
The medical field is witnessing a paradigm shift towards miniaturized devices. From implantable monitors to drug delivery systems, smaller sizes often mean less invasiveness, greater comfort, and higher efficiency. However, as the size of these devices decreases, the challenge of manufacturing complex components also increases. Advanced stamping technology is revolutionizing the way we achieve miniaturization in medical devices:
Greater Detail and Precision: When it comes to the minute details required for micro-medical devices, traditional stamping methods may fall short. Advanced technologies, especially micro-stampings, can produce parts with extremely fine details. This precision ensures that even the smallest components function optimally, which is a critical factor when slight deviations can affect the performance of the device or the health of the patient.
Reducing Waste of Expensive Medical-Grade Metals: In the medical field, the metals used are not just any metals. They are typically of high quality and biocompatible, thus expensive. Advanced stamping technologies are more efficient, ensuring that every bit of material is used optimally. This not only reduces costs but also aligns with the growing emphasis on sustainability in the medical industry.Production of Complex Equipment Components: Taking a pacemaker as an example, it is a marvel of medical engineering. It is small enough to be implanted near the heart, yet it contains a battery, electronic circuits, and leads inside. Or consider a hearing aid, which integrates advanced technology into a device small enough to be fitted inside or behind the ear. Manufacturing the metal parts of such devices requires advanced stamping techniques that can produce complex parts with impeccable precision.
Cost Implications
In the realm of complex medical devices, precision is combined with life-saving functions, and a delicate balance must be struck between ensuring top-notch quality and managing costs. While there can be no compromise on the former, understanding cost implications can lead to wiser decisions and efficient production. Here is a detailed analysis of the factors that play a key role in determining the cost of metal stamping components for medical devices:
Material Selection: The type of metal or alloy chosen directly affects the cost. While medical-grade metals have undeniable advantages due to their biocompatibility and durability, there are still multiple options. For instance, titanium may be more expensive than certain grades of stainless steel, but its strength and corrosion resistance may justify the cost for specific applications.
Complexity of Stamped Parts: The cost of a simple flat component is always lower than that of a complex multi-dimensional part. Advanced techniques for complex designs, such as micro-stampings or deep drawing, may also increase costs. The number of processes a part must undergo (from stamping to finishing) will also affect the final price.
Production Volume: Economies of scale play a significant role in metal stamping. Producing a large number of parts in one run can reduce the per-unit cost. This is because certain fixed costs (such as machine setup or design modifications) are spread over more parts. However, it is necessary to balance quantity with demand to avoid overproduction and waste.
Case Studies: Successful Implementation of Medical Device Stamping
Exploring the complex world of medical device stamping is by no means an easy task. With patient safety at stake, manufacturers are constantly pushing the envelope to achieve unparalleled precision and reliability. Let's delve into some renowned case studies that showcase success and innovation in this field:Medtronic's Microstamping Technology: Medtronic, a global leader in medical technology, faced the challenge of producing ultra-precise components for its most advanced pacemakers. By adopting advanced microstamping techniques and investing in rigorous quality checks, they successfully achieved consistent accuracy, even at microscopic scales. Their success story underscores the importance of embracing cutting-edge technology to meet the ever-evolving demands of healthcare.
Johnson & Johnson's Journey with Biocompatible Metals: When Johnson & Johnson ventured into the production of orthopedic implants, material selection was crucial. They chose titanium alloy, highly regarded for its strength and biocompatibility. However, stamping this alloy posed challenges due to its strength. Through innovative mold design and specialized stamping processes, they achieved a perfect blend of durability and biocompatibility.
Boston Scientific and the Sterilization Challenge: Known for its diverse range of medical devices, Boston Scientific encountered a challenge with a particular stamping component that showed signs of degradation after sterilization. Upon in-depth investigation, it was found that the metal's chemical composition reacted adversely to the sterilization process. By adjusting the alloy mixture and improving the stamping process, they not only solved this issue but also enhanced the overall durability of the components.
Stryker's Cost-Effective Stamping Solutions: Although Stryker is renowned for its high-quality medical devices, they also faced the universal challenge of managing costs. By optimizing output, selecting cost-effective and reliable materials, and streamlining the stamping process, they successfully balanced quality and cost, setting an industry benchmark.
---
The Future: Innovation on the Horizon
The field of medical device stamping is constantly evolving, with groundbreaking innovations emerging every year. As we stand on the cusp of a new era, let's delve into some of the most promising trends and technologies that will redefine the landscape:
Smart Materials—Beyond Just Metals: Imagine a stent that expands or contracts in response to blood flow, or an implant that releases medication upon detecting inflammation. The future will see the use of smart materials in metal stamping that can sense and adapt to the body's dynamic conditions, providing tailored therapeutic effects.
Electronic Integration—The Rise of Smart Implants: The boundary between electronic products and medical devices is blurring. Upcoming stamped components will not only be passive structures but also accommodate miniaturized electronic devices, sensors, and even communication modules. Consider implants that can transmit real-time data to physicians or devices that can be remotely adjusted post-surgery.
Rapid Prototyping—Accelerating Innovation: The medical field demands constant innovation. With advancements in rapid prototyping, the journey from concept to tangible device has never been faster. This not only accelerates device development but also enables real-time testing and iteration, ensuring that the final product is flawless.Customized Stamping — Tailor-Made for Individuals: With the rise of personalized medicine, there is a growing demand for medical devices that are tailored to individual patients. Advanced stamping techniques combined with detailed medical imaging will enable the production of implants and devices that fit the patient's anatomy with unparalleled precision.
Conclusion
Sheet metal stamping in the medical device field is a delicate balance between precision, quality, and cost-effectiveness. As technology advances and the demand for more complex devices grows, the industry must continue to evolve to ensure that patient safety and device efficacy remain at the forefront.
Comment