The magic of Computer-Aided Design (CAD) can often lead designers to believe in boundless possibilities. However, the reality of metal stamping brings with it a series of challenges. Collaborating with metal stamping engineers in the early stages of the design process can bridge this gap.
While precise, metal stamping also has its limitations. The characteristics of materials, such as thickness, hardness, and grain orientation, play a significant role in the final product. Common materials include ferrous metals, non-ferrous metals, stainless steel, and more. Engineers can guide manufacturers in selecting the right materials to ensure they meet requirements and avoid issues such as cracking.
Understanding the nuances of metal stamping can prevent costly mistakes and ensure a smoother production process.
Material Selection and Its Impact
In the field of metal stamping, the choice of material is crucial. It is not just about selecting a type of metal, but understanding its properties, its interaction with the stamping process, and the requirements of the final product. The characteristics of materials can significantly impact the outcome, making it necessary to delve into the roles of different metals and the guidance experts can provide.
Advertisement
The Role of Different Metals
Metal stamping is a versatile process suitable for various metals, each with its unique characteristics.
The characteristics of metals and their impact on stamping results:Every type of metal, whether it be ferrous metals, non-ferrous metals, stainless steel, or aluminum, possesses its own unique characteristics. For instance, the hardness of a metal can determine its ductility during the stamping process. The grain orientation of the metal can affect the strength of the final product, while the thickness of the metal can impact its formability. Understanding these subtle differences is crucial for achieving the desired outcomes.
Typical materials used in stamping:
The world of metal stamping is vast, with a plethora of materials to choose from. Commonly used materials include:
Ferrous and non-ferrous metals: These are metals that contain iron and those that do not, respectively. Each category of materials has its own advantages; ferrous metals are more magnetic, while non-ferrous metals are more corrosion-resistant.
Stainless steel: Known for its corrosion resistance and strength.
Aluminum: Lightweight and highly malleable, making it very suitable for complex designs.
Titanium and precious metals: Renowned for their durability, corrosion resistance, and oxidation resistance.
Pre-coated metals and polyester films: Provide additional protection or specific characteristics for stamped parts.
Metal wires: Used for specific applications that require flexibility.Expert Guidance on Material Selection
Choosing the right material is only half the battle. Ensuring that the material meets the design and production requirements is where the value of expert guidance truly lies.
The Importance of Consulting with a Metal Stamping Engineer:
The specialized knowledge of engineers can bridge the gap between design aspirations and production realities. They can gain an in-depth understanding of how materials behave during the stamping process, ensuring that the final product meets the expected specifications without compromising quality or functionality.
Potential Issues with Certain Materials and Possible Alternatives:
Not all metals are created equal. Some materials may be prone to issues such as cracking during the stamping process. For instance, materials that are too brittle may not be suitable for designs requiring high ductility. In such cases, a metal stamping engineer can propose alternative solutions that better align with the design requirements. Their experience can help manufacturers avoid costly mistakes and production delays, ensuring a smoother transition from design to the final product.
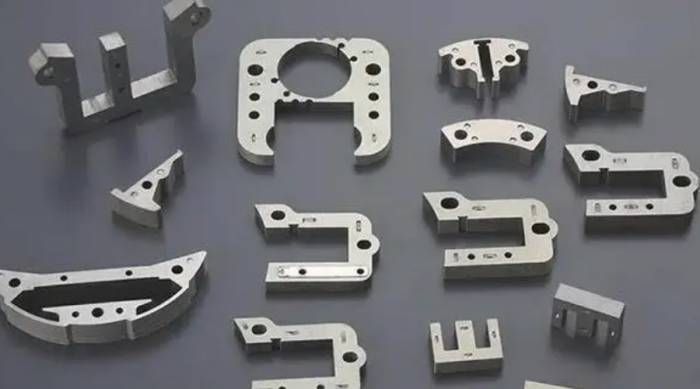
Debunking Misconceptions about Metal Stamping
Metal stamping, while a versatile and efficient process, is often misunderstood. Some common misconceptions can lead to costly errors or suboptimal outcomes. By addressing these misconceptions head-on, we can ensure that metal stamping projects proceed more smoothly and wisely.Replacing Other Materials and Processes
The allure of metal stamping often leads people to believe that it can perfectly replace other materials and processes. However, the reality is more nuanced.
Challenges in Replacing Molded or Cast Parts with Metal Stampings:
While metal stampings are characterized by precision and high efficiency, they are not a one-size-fits-all solution. Molding and casting have their unique advantages, and directly replacing them with stampings may present challenges. For instance, complex parts formed from plastic may not easily translate into metal stampings due to differences in material properties and production techniques.
Real-world examples illustrate the complexities involved:
For example, a manufacturer wishes to replicate a plastic-molded part with metal stamping. A complex design that is easily achievable in plastic molding comes at a high cost in metal stamping. It requires multiple die stations, increasing production time and costs. If willing to make slight adjustments to the design, production efficiency might be higher without compromising functionality.
Addressing Critical Dimension Issues
Precision is at the core of metal stamping. However, unclear critical dimensions or last-minute changes can pose challenges.
Clarifying Critical Dimensions from the Start:
It is essential to define critical dimensions from the outset:When designing metal stamping parts, it is crucial to determine the critical dimensions as early as possible. These dimensions are vital for the functionality and fit of the parts. By pre-determining these dimensions, metal stamping factories can ensure that the molds and production processes are aligned with these specifications, thereby producing parts that meet or exceed expectations.
Potential cost implications of late changes:
Altering critical dimensions after the mold design or even manufacturing is complete can be costly. This not only requires changes to the mold but may also lead to production delays. For instance, if the design of a part has been finalized and the mold has been made, but later the quality department expands the list of critical dimensions, this may necessitate mold modifications. Such modifications can increase costs and extend production time, thus emphasizing the importance of clear communication and thorough planning from the outset.
Precision and tolerances in design
Achieving precision in metal stamping is a delicate balance between design aspirations and manufacturing realities. Understanding the nuances of tolerances and the tools used in the design process is essential for ensuring the functionality and cost-effectiveness of the final product.
The role of CAD
Computer-Aided Design (CAD) has revolutionized the way we visualize and plan manufacturing. However, it is also crucial to recognize its limitations and potential pitfalls.
CAD can sometimes lead to overly tight tolerances:The precision of CAD software can sometimes lead designers to have a mistaken understanding of what can be achieved in the real world. While it is possible to design parts with extremely tight tolerances on the screen, replicating these precise measurements in metal stamping can be difficult and costly. For instance, CAD might default to a certain number of decimal places, which is achievable on the screen but may not be practical for mass production.
It is crucial to have realistic and cost-effective specifications:
Pursuing perfection is commendable, but a balance must be struck between design aspirations and practicality. Excessive tolerance requirements can lead to increased production costs without necessarily enhancing the value of the final product. Collaborating with metal stamping experts during the design phase helps align CAD designs with real-world conditions, ensuring a smoother production process and products that meet expectations without incurring unnecessary costs.
Designing safe and practical edges
The edges and corners of metal stampings play a vital role in their functionality and safety. These aspects must be carefully designed to ensure that the parts perform their intended functions without posing risks.
Challenges with specifying sharp edges and corners:
Sharp edges and corners can pose safety hazards, especially during assembly or when parts need to be handled in their final application. Moreover, overly sharp designs can also present challenges in the stamping process, such as increasing die wear or raising the likelihood of defects.
Recommendations for safer and more practical designs:
Designers should not default to "removing all sharp edges and corners," but rather specify which areas of the part require specific edge conditions based on functional requirements. For example, if a sharp corner could pose a risk of cutting or wearing down another component, specifying a rounded edge in that area might be beneficial. Collaborating with metal stamping experts can provide insights into the best edge designs that balance safety, functionality, and manufacturability.Adopting Design for Manufacturability (DFM)
Design for Manufacturability (DFM) is a proactive design approach that ensures a product is not only functional and aesthetically pleasing but also easy to manufacture and cost-effective. By considering manufacturing constraints and opportunities early in the design process, DFM can lead to better products, faster time to market, and reduced production costs.
Comprehensive DFM Review
A comprehensive DFM review is crucial for identifying potential manufacturing challenges and opportunities early in the design process. This review ensures that the design is optimized for efficient and economical production.
A robust DFM review process includes the following steps:
Reviewing customer specifications: Understanding the intended application, expected lifespan, and any special requirements of the part.
Regulatory and statutory requirements: Ensuring the design complies with any relevant industry standards or regulations.
Evaluating materials and their properties: Selecting appropriate materials based on the part's function and the required production method.Consideration of Tools: Ensure that the use of existing tools and machinery can efficiently produce the design.
Final Assembly and Packaging Requirements: Consider how to assemble the parts into the final product, as well as any packaging or transportation constraints.
The Importance of Cooperation Between Manufacturers and Metal Stamping Companies:
Cooperation can ensure that both parties have a clear understanding of the design objectives and limiting factors. Metal stamping companies can provide valuable insights on the manufacturability of the design, while manufacturers can clarify any functional or aesthetic requirements. This collaborative approach can lead to more rational design decisions, fewer modifications, and a smoother production process.
The Role of Prototyping in the DFM Process:
Prototyping is an essential tool in the DFM process, allowing manufacturers to test and validate their design before moving into full-scale production.
When and Why to Consider Prototyping:
If there is uncertainty about how the design will perform under actual conditions, a prototype can provide valuable insights.
For complex or innovative designs, a prototype can identify any unforeseen challenges or opportunities.Before committing to mass production, prototypes can also be used to test the market's reaction to new products.
Advantages of simulation software in assessing the feasibility of designs:
Simulation software can model the performance of a design under various conditions, identifying potential weak points or areas for improvement.
By simulating the manufacturing process, designers can discover and address potential production challenges early in the design process.
Using simulation software can reduce the need for physical prototypes, thereby saving time and money. However, when physical validation is essential, the combination of simulation and prototype design can provide a comprehensive understanding of the feasibility of the design.
Conclusion
Understanding the nuances and limitations of metal stamping from the design phase can improve the efficiency of the production process, saving time, money, and resources. Through collaboration and expert guidance, it can be ensured that the design is innovative and manufacturable.
Comment