High-speed stamping has revolutionized the manufacturing landscape, but it also brings a host of challenges. How can the process be optimized to achieve the highest efficiency and the longest service life? Delve into some valuable tool tips for a deeper understanding.
In high-speed stamping applications, it is crucial to use the polished length rather than the material thickness to determine the offset. This method can minimize punch wear, reduce wire drawing, and provide more feed time, thereby enhancing the efficiency of the entire stamping process.
To fully grasp the significance of this tip and explore more insights into high-speed stamping dies, let's delve deeper.
The Importance of Polished Length in High-Speed Stamping
In the realm of high-speed stamping, precision and efficiency are paramount. In the pursuit of these goals, "polished length" is one of the critical factors. But what exactly is polished length, and why is it so important?
Understanding Polished Length
Polished length refers to the polished portion of the stamping edge, which is typically the result of the interaction between the tool or die and the metal during the stamping process. This polished part is a clear indicator of the quality of the stamping process. Material thickness can vary, while polished length provides a more consistent and reliable measure. It is a subtle yet significant aspect that can greatly influence the outcome of the stamping process.
Advertisement
Advantages of Using Polished Length Over Material Thickness:
There are several benefits to choosing polished length over material thickness, including:
1. **Consistency**: Polished length offers a more consistent measurement, which is less susceptible to the variations that can occur with material thickness.
2. **Predictability**: It allows for more predictable tooling performance, as it accounts for the actual condition of the stamping edge rather than just the material's thickness.
3. **Reduced Wear**: By basing the offset on polished length, the wear on the punch is more evenly distributed, which can extend the life of the tooling.
4. **Improved Quality**: A focus on polished length can lead to higher quality stampings, as it ensures that the process is optimized for the specific characteristics of the material being used.
5. **Efficiency**: The use of polished length can streamline the stamping process, as it reduces the need for adjustments and rework due to variations in material thickness.
By incorporating these insights into your high-speed stamping operations, you can enhance the overall performance and longevity of your tools and processes.Reduce Punch Wear: By focusing on the polishing length, the interaction between the punch and the material becomes more controllable, thereby reducing wear. This not only extends the service life of the punch but also ensures the consistent quality of the stamped products.
Increased Feed Time: Attention to the polishing length minimizes the interaction time between the punch and the material. The reduction in interaction time can speed up the feed time and optimize the overall stamping speed.
Quality Stability: Compared to material thickness, which may vary due to various factors, the polishing length provides a more consistent measurement. This consistency ensures that each stamped product meets the required quality standards.
Practical Significance
One of the most notable practical applications of emphasizing polishing length in high-speed stamping comes from the automotive industry.
Toyota is a leading global automotive manufacturer facing challenges in its stamping process. They found that the quality of the stamped parts was unstable, leading to rework and material waste, which increased production costs. After in-depth analysis, their engineering team discovered that relying solely on material thickness was the root cause of these inconsistencies.
To address this, Toyota shifted its focus to the polishing length. By doing so, they achieved:
Improved Product Quality: The consistency of the stamped parts significantly improved, with the number of defective products reduced by nearly 18%.
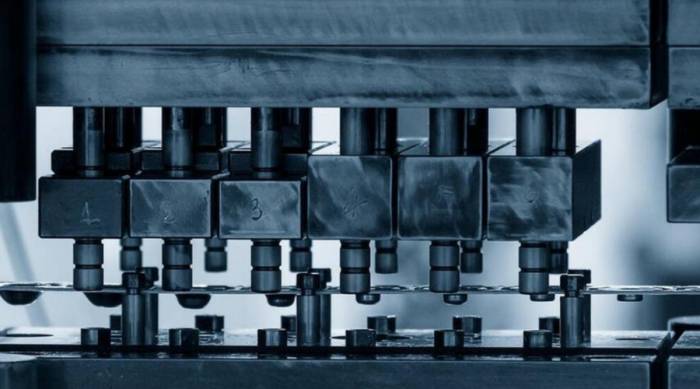
Extended Tool Life: The wear on stamping tools was reduced, extending the tool life by 25%, thus saving a considerable amount of cost.
Optimized Production Speed: Due to the shortened interaction time between the punch and the material, the production line speed increased by 15%, thereby increasing output.Toyota's shift to emphasizing the importance of polishing length has proven the practical advantages of this method in high-speed stamping. Their success story has inspired many other manufacturers to re-evaluate their stamping processes.
Other fundamental tool tips for high-speed stamping
High-speed stamping is a complex process, and while polishing length plays a crucial role, there are other equally important factors to consider. Let's delve into these essential die techniques that can play a significant role in the stamping process.
Tolerance levels in high-speed stamping
Tolerance in manufacturing refers to the permissible limits of physical size variation. In high-speed stamping, maintaining strict tolerances is essential for ensuring the consistency and quality of stamped parts.
The importance of precision: In industries such as aerospace or medical devices, even a minor deviation from the required dimensions can render a part non-functional or even unsafe. Therefore, achieving and maintaining precision is unquestionable.
Ensuring the required tolerances: Modern stamping machines are equipped with sensors and feedback systems that continuously monitor the dimensions of stamped parts. Any deviation from the set tolerance levels can be immediately corrected, ensuring consistent quality.
Challenges: Factors such as tool wear, material inconsistencies, or temperature fluctuations can affect tolerances. Regular maintenance, quality inspections, and the use of high-quality materials can mitigate these challenges.Tool Wear Monitoring and Predictive Maintenance
The service life and performance of stamping tools are crucial for maintaining production efficiency and quality.
Monitoring Technology: Advanced sensors can detect minor changes in tool performance, thereby indicating wear conditions. Acoustic, vibration, and force sensors are commonly used for this purpose.
Predictive Maintenance: Predictive maintenance uses data from monitoring systems to predict when tools may fail or require maintenance, rather than waiting for a tool to fail. This approach can reduce downtime and ensure uninterrupted production.
Benefits: By proactively addressing tool wear issues, manufacturers can reduce production costs, improve product quality, and extend the service life of tools.
Thermo-Dynamics in High-Speed Stamping
Heat generation is a natural byproduct of high-speed operations, and managing it is essential for maintaining quality and efficiency.
Sources of Heat: Friction between tools and materials, material deformation, and the rapid movement of mechanical parts are the main sources of heat generation in the stamping process.
Heat Management: Effective cooling systems, such as liquid coolants or jets, can dissipate the heat generated. Choosing materials with better thermal properties can also be helpful.
Impact of Uncontrolled Temperature: Overheating can lead to tool wear, material deformation, and even tool failure. It can also affect the performance of the material, resulting in inconsistent stamping parts.High-Speed Stamping Case Study
High-speed stamping is a complex process, with different companies adopting unique strategies to optimize their operations. Let's explore some practical cases to highlight the practical application of the discussed die techniques.
Bosch's Success in Polishing Length
Bosch, a global leader in technology and service provision, faced the challenge of maintaining consistent quality in high-speed stamping operations for automotive components. They found that relying on material thickness led to inconsistencies.
After shifting their focus to burnishing length, Bosch discovered new solutions:
Improved product quality: The consistency of stamped parts increased by 20%, reducing the number of defective products.
Extended tool life: The wear on stamping tools was reduced, extending the tool life by 30%.
Optimized production speed: The production line speed was increased by 18%.
Siemens' Tool Wear Monitoring Method
Siemens, a multinational conglomerate, has developed a tool wear monitoring method that has significantly improved the efficiency and reliability of their high-speed stamping processes.
By implementing advanced sensor technology and data analysis, Siemens has been able to:
Predict tool wear more accurately: The use of predictive analytics has allowed for more precise forecasting of tool wear, leading to better maintenance planning.
Reduce downtime: With real-time monitoring, Siemens can address tool issues before they lead to production stoppages, minimizing downtime.
Enhance product quality: By maintaining optimal tool conditions, the consistency and quality of the stamped products are consistently high.
These case studies demonstrate how companies like Bosch and Siemens leverage innovative approaches to enhance their high-speed stamping operations, leading to improved product quality, extended tool life, and optimized production efficiency.Siemens is a multinational corporation specializing in the fields of electrification, automation, and digitalization, and has adopted an advanced tool wear monitoring system in its high-speed stamping operations for electronic components.
By employing acoustic and vibration sensors, the system can monitor tool wear:
Reduce downtime: Predictive maintenance has reduced machine downtime by 25%.
Extend tool life: A proactive approach has extended tool life by 40%.
Improve product quality: The consistency and quality of the stamped parts have increased by 15%.
GE Appliances' Thermal Management Solutions
GE Appliances is a well-known manufacturer of electrical appliances, facing challenges in thermal management during its high-speed stamping operations. Excessive heat leads to tool wear and material inconsistency.
After adopting an advanced cooling system and selecting materials with better thermal performance, GE Appliances' thermal management solution has achieved significant results:
Reduce tool wear: Tool wear has been reduced by 20%.
Improve product consistency: The consistency of the stamped parts has increased by 25%.Enhancing Worker Safety: Controlled temperatures reduce the risk of accidents related to high temperatures in production facilities.
Improving the Efficiency of High-Speed Stamping
High-speed stamping is the cornerstone of many manufacturing processes, and its efficiency directly affects productivity, quality, and overall profitability. As the industry evolves, so do the methods for improving efficiency. Let's delve into some key strategies that companies have adopted to optimize high-speed stamping operations.
The Role of Automation
In the era of Industry 4.0, automation has transformed many manufacturing processes, including high-speed stamping.
Precision and Consistency: Automation systems driven by advanced algorithms ensure the precision of each stamping action, thereby reducing the likelihood of defects and waste.
Increased Productivity: Compared to manual operations, automation systems can operate continuously without fatigue, thus increasing productivity.
Adaptability: Modern automation systems can quickly adapt to changes, whether it's new designs or materials, ensuring that production does not lag during transitions.
Companies like ABB and Fanuc have been at the forefront, offering robotic solutions that seamlessly integrate with high-speed stamping operations, thereby enhancing output and quality.Quality Control Measures
In the high-speed stamping process, ensuring stable quality is crucial, as even minor defects can lead to significant losses.
Real-time Monitoring: Advanced sensors and cameras can monitor the stamping process in real-time, detecting and correcting anomalies instantly.
Feedback Loops: Modern stamping machines are equipped with feedback systems that adjust operations based on the quality of the output, ensuring the minimization of defects.
Post-production Inspection: Automated post-production quality checks using technologies such as computer vision can detect and isolate defective parts, ensuring that only top-quality products reach the market.
Samsung has always been a pioneer in implementing strict quality control measures in its production processes, including high-speed stamping, ensuring that its products consistently meet high standards.
Training and Skill Development
While automation and quality control are essential, the human factor remains critical in high-speed stamping operations.
Skill Development: Regular training ensures that operators are familiar with the latest technologies and best practices in stamping.
Safety Training: High-speed operations carry certain risks. Safety training ensures that operators can safely handle machinery, reducing the likelihood of accidents.Soft Skills: Training operators in soft skills such as problem-solving and critical thinking ensures that they can effectively handle unforeseen challenges.
Toyota, renowned for its famous Toyota Production System (TPS), places great emphasis on continuous skill development, ensuring that its employees are always equipped to handle the challenges of high-speed stamping.
Conclusion
High-speed stamping is a testament to the marvels of modern manufacturing, where precision, speed, and efficiency come together to produce complex parts that are widely used in many products we use daily. At the core of this intricate process is the concept of the polishing length, a seemingly subtle detail that has a profound impact on the quality and consistency of the stamped parts.
By optimizing the interaction between the punch and the material, the polishing length not only ensures that each stamped part meets strict standards but also extends the tool's lifespan, making the entire process more sustainable and cost-effective. This is a prime example of how attention to detail can significantly improve manufacturing processes.
However, in the dynamic world of manufacturing, complacency is not an option. Driven by technological advancements, changing consumer demands, and shifts in the global economy, the industry is in a state of constant evolution. In this context, the importance of continuous learning and adaptation cannot be overstated. Whether it is embracing automation, investing in quality control, or enhancing employee skills, staying ahead is imperative.
Finally, while the polishing length gives us a glimpse into the complex world of high-speed stamping, it also serves as a reminder. It reminds us that in the intricate dance of machines, metals, and human ingenuity, it is often the subtle differences that make all the difference. Looking ahead, it is these subtle differences, coupled with a spirit of continuous innovation, that will write the next chapter of manufacturing.
Comment