Metal stamping is the cornerstone of the manufacturing industry; it not only shapes materials but also affects the core of the material—microstructure. But how profound is this influence, and what does it mean for the final product? Let's delve deeper into this.
Metal stamping can cause changes in the material's microstructure, which may affect its mechanical properties such as hardness, tensile strength, and ductility.
To truly understand the impact of these changes, we need to explore the science behind the stamping process and its effects on the material at the microscopic level.
Microstructure Science
The microstructure of a material is like the DNA of the material, determining its characteristics and behavior under various conditions. Often overlooked, its impact on manufacturing and materials science is profound.
What is Microstructure?
The microstructure of a material refers to the internal structure observed under a microscope. It pertains to the arrangement, size, and distribution of material components at the microscopic scale. For metals, this typically refers to the arrangement and size of grains (or crystallites) and the nature of grain boundaries. Microstructure plays a key role in determining the mechanical, electrical, thermal, and magnetic properties of materials. For instance, the strength and ductility of steel can vary greatly due to different microstructures, which is why processes like tempering and annealing, which alter microstructures, are so important in metallurgy.
Advertisement
Factors Affecting Microstructure
Several factors come into play when determining the microstructure of a material:
1. **Composition**: The type and amount of elements present in the material can significantly influence its microstructure.
2. **Processing**: The methods used to process the material, such as casting, forging, or rolling, can affect the grain size and shape.
3. **Heat Treatment**: Processes like quenching, annealing, and tempering can alter the microstructure by changing the arrangement of atoms and the formation of different phases.
4. **Cooling Rate**: The rate at which a material cools after processing can lead to different microstructures, as rapid cooling can lock in defects or create fine-grained structures.
5. **Stress and Strain**: The application of stress and strain during the stamping process can cause dislocations in the material's crystal lattice, which can change the microstructure.
Understanding these factors and how they interact is crucial for controlling the microstructure and, consequently, the properties of the material. This knowledge is essential for optimizing the stamping process to produce parts with the desired characteristics for various applications.Grain Size: The size of individual grains in a material can affect properties such as strength and ductility. Generally, the smaller the grains, the higher the strength.
Microstructure: Many materials consist of multiple phases. For example, carbon steel contains ferrite and cementite phases. The distribution, size, and composition of these phases can greatly influence the properties of the material.
Defects: No material is perfect. Defects such as dislocations, vacancies, and interstices may exist within materials. These defects can be either harmful, leading to weak points, or beneficial, as in certain alloys where controlling defects can enhance strength.
Grain Boundaries: Grain boundaries are the interfaces where grains of different orientations meet. They can act as barriers to dislocation motion, affecting the mechanical properties of the material.
Understanding the factors that influence microstructure is crucial, especially when processes like metal stamping come into play, potentially altering these factors.
Metal Stamping: A Brief Overview
Metal stamping may seem simple, but it is actually a dance of precision, force, and material science. It is not just about shaping metal, but understanding the nature of the metal and its response under pressure.
Basics of Metal Stamping
Metal stamping is a cold forming process that involves placing a sheet of metal into a press that has tooling and die surfaces, shaping the metal into the desired form. This technique is widely used across various industries from automotive to electronics, producing parts we encounter daily, such as car body panels or electronic connectors. However, there is a subtle difference: the thickness, temperature, and even surface finish of the metal sheet can affect the outcome of the stamping process. A slight change in any of these factors can lead to defects such as warping or tearing.The Action of Forces
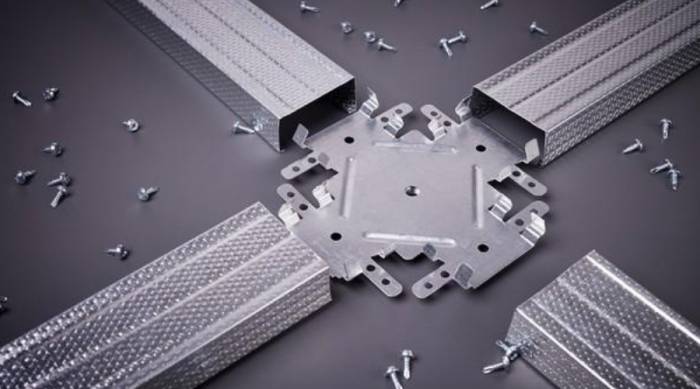
At first glance, stamping may appear to be merely the application of simple forces. However, upon closer examination, you will discover a symphony of stress and strain being played out:
Direct Compression: The most apparent force, where metal is directly compressed between dies and tools, thereby taking on the shape of the mold.
Tensile Stress: As the metal is compressed, portions of it are also stretched. This stretching generates tensile stress, which, if not controlled, can lead to metal tearing.
Shear Stress: This type of stress occurs on the surface of the metal, especially where the metal slides against the mold. Excessive shear forces can result in surface defects.
Strain Hardening: When metal undergoes deformation, its grains are compressed and elongated, causing the material to harden. This phenomenon affects the final properties of the stamped parts.
Springback: After stamping, the metal, due to its inherent elasticity, tends to slightly revert to its original shape. This "springback" needs to be considered in die design to ensure the precision of the final components.
The interplay of these forces and the material's response to them demonstrate the complexity of the stamping process. Stamping is not just about shaping; more importantly, it is about understanding and utilizing various forces to achieve precision and quality.
Impact on the Final ProductAlthough the primary purpose of metal stamping is to shape the material, the impact of this process extends far beyond mere form. The act of stamping itself alters the microstructure of the material, thereby significantly affecting the performance and durability of the final product.
Changes in Mechanical Properties
At first glance, a stamped metal part may appear identical to its original form, but beneath the surface, there may have been dramatic changes:
Strength and Hardness: The deformation during the stamping process leads to strain hardening, where metal grains are compressed and elongated. This can enhance the material's strength and hardness, which may be beneficial in some applications but detrimental in others where ductility is required.
Ductility: As mentioned, strain hardening reduces the material's ductility, making it less capable of stretching without breaking, and more prone to cracking under certain conditions.
Residual Stresses: The stamping process generates internal stresses within the material. While these stresses may not manifest immediately, they can lead to warping or premature failure under specific conditions.
Grain Orientation: During the stamping process, the alignment of metal grains changes. This orientation affects properties such as tensile strength and electrical conductivity.
Durability and Performance
The microstructural changes induced by stamping do not remain on paper; they manifest in the real world, affecting the performance of stamped parts:
Wear Resistance: Changes in hardness and grain orientation affect the rate at which parts wear during use.Corrosion Resistance: Residual stresses and microstructural defects can become the starting points for corrosion, especially when metals are exposed to corrosive environments.
Fatigue Life: Components subjected to cyclic loads (repeated stress) can experience fatigue. The microstructural changes induced by stamping can either enhance or diminish the part's resistance to fatigue.
Thermal Properties: The way a material conducts heat is influenced by its microstructure. This can be an important consideration for parts operating in high-temperature environments.
The charm of metal stamping lies in its forming capabilities, but the art is in understanding and controlling the myriad of subtle changes that occur beneath the surface, ensuring that the final product is not only visually correct but also performs optimally.
Summary
Metal stamping is the cornerstone of the world's manufacturing industry; it is more than just a metal forming process. It is a journey that the material undergoes, and the transformations it experiences at the micro level can have profound effects on its macroscopic properties.
The act of stamping may seem simple, but it is a dance of forces and reactions. During the metal forming process, the microstructure—such as the arrangement of grains, the presence of defects, and the orientation of metallography—undergoes changes. These changes are often subtle and invisible, yet they can determine the material's strength, ductility, corrosion resistance, and even thermal properties.
But what does it matter? Because in the fields of engineering and design, every detail counts. The performance, durability, and intended function of a component depend on understanding these subtle differences in microstructure. Whether it's the body panels of a car, electronic connectors, or simple household items, the changes induced by stamping can be the key to whether a product is excellent or not.
For those involved in metal stamping projects, recognizing this complex relationship is crucial. It is not only about the correct shape but also about ensuring that the material's essence and microstructure match the desired characteristics and performance. Only then can the full potential of metal stamping be realized, creating products that are not only aesthetically pleasing but also functionally superior.In the final analysis, metal stamping is a testament to the beauty of manufacturing—where art and science merge perfectly, with every stamping, bending, and folding telling a story of transformation.
Comment