The metal stamping project is a complex dance of design, precision, and execution. Let's unravel the lifecycle of these projects from the initial concept to the final product.
The lifecycle of a metal stamping project encompasses every stage from the design conception, material selection, prototyping to the final production, ensuring accuracy and quality at every step.
Delve into the intricate processes and innovations that bring metal stamping projects to life.
Conceptualization and Design
Every metal stamping project begins with an idea, a vision. This initial phase is often overlooked but is the foundation of the entire project. It is where dreams are translated into actual designs, and it is where the journey from concept to realization truly begins.
Understanding Customer Requirements and Project Objectives
Before any metal enters the stamping press, it is crucial to understand the true needs of the customer. This requires comprehensive discussions, with every detail, no matter how minute, being carefully considered. Questions such as "What is the final use of the stamped part?", "Are there specific weight or strength considerations?", and "What is the expected production volume?" are all addressed. This phase ensures that the project aligns with the customer's vision and objectives, setting a clear roadmap for subsequent stages.
Advertisement
Preliminary Sketches, CAD Designs, and Feasibility Analysis
Once the requirements are very clear, the design phase begins. Preliminary sketches are drawn, providing a rough visual representation of the final product. These sketches are then translated into detailed CAD (Computer-Aided Design) models, offering a three-dimensional perspective and allowing for complex detail handling.But design is not just about aesthetics. It also concerns functionality and feasibility. After the CAD design is completed, a feasibility analysis must be conducted. This step takes into account factors such as material properties, mold limitations, and production costs to assess whether the design can be practically stamped. This is a crucial phase where not only the aesthetic appeal of the design is ensured but also its manufacturability.
Essentially, the conceptualization and design phase is a fusion of creativity and pragmatism. During this stage, the client's vision is combined with the realities of production, laying the groundwork for the magic of metal stamping to unfold.
Material Selection
In the field of metal stamping, the choice of material is of paramount importance. It is not just about selecting a metal, but choosing the right one that perfectly aligns with the project objectives. This decision affects everything from the manufacturing process to the performance of the final product.
Selecting the appropriate metal based on project requirements
Different projects have different needs. Components designed for aerospace applications have vastly different requirements compared to those designed for household appliances. Factors such as corrosion resistance, conductivity, thermal properties, and weight play significant roles in the decision-making process.
For example:
Aluminum is lightweight and corrosion-resistant, making it a preferred choice for automotive and aerospace applications.
Stainless steel is known for its strength and rust resistance, making it a top choice for medical devices and kitchen utensils.Copper has excellent electrical conductivity, making it the preferred choice for electrical connectors and circuits.
The choice is not always that simple. Alloys are often selected, which are combinations of two or more metals, to take advantage of the best characteristics of each constituent metal.
Consider strength, flexibility, and ultimate use
Each metal has its unique properties. Some metals are hard and rigid, while others possess ductility and flexibility. The key is to match these properties with the project requirements.
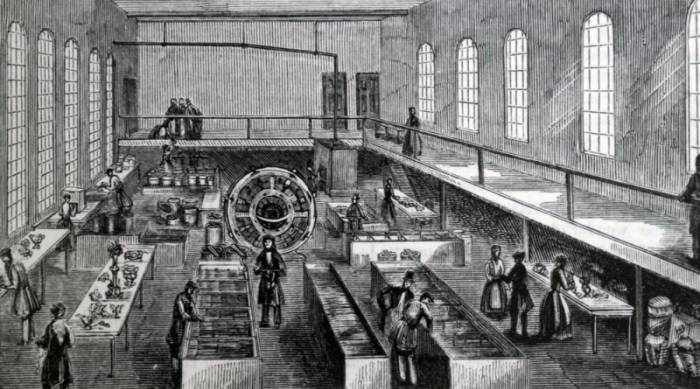
Strength: For components that need to withstand loads or stresses, metals with high tensile strength are preferred. This ensures that the components do not deform or break under pressure.
Flexibility: Some projects, especially those requiring complex designs or deep drawing, need metals that can be bent into shape without breaking. These applications require metals with good ductility.
Ultimate use: The environment in which the final product will be used also determines the choice of material. For example, components exposed to seawater may require metals that are resistant to seawater corrosion. Similarly, components used in high-temperature environments also need metals that can withstand high temperatures without losing their properties.
In summary, material selection is a delicate balance of science and art. It requires a deep understanding of metallurgy and a clear understanding of project goals. The right material choice ensures that the final stamped components are not only aesthetically pleasing but also perform flawlessly in their intended applications.
Prototyping and testingOnce the design and materials are determined, the next key step in the life cycle of a metal stamping project is the creation of prototypes. At this stage, theory and practice are combined to transform ideas into tangible samples, ready for rigorous testing.
Creating Initial Samples for Validation
Prototype design serves as a bridge between design and mass production. It is the process of creating a limited number of samples that represent the final product. These prototypes serve multiple purposes:
Validation of Design: Prototypes bring CAD designs to life, allowing for practical assessment. They help to identify any discrepancies between the design and the actual product.
Functional Testing: Beyond aesthetics, prototypes can also be used to test whether the functionality of the components meets expectations. Does it fit where it is supposed to? Can it effectively perform its intended task?
Gathering Feedback: Prototypes can be shared with stakeholders, including customers, to collect feedback. This early feedback is invaluable for making necessary adjustments before mass production.
Stress Testing, Durability Assessment, and Design Improvement
Once the prototypes are ready, they undergo a series of rigorous tests:
Stress Testing: These tests subject the prototypes to the forces and pressures they are likely to encounter during their service life. The aim is to ensure that the components can withstand these stresses without deforming or breaking.
Durability Assessment: How long will the component last? Durability tests often involve repeated use or exposure to harsh conditions, helping to answer this question. For metal stampings, this may involve repeated bending, exposure to corrosive environments, or temperature fluctuations.Design Improvements: Based on test results and collected feedback, the design may require adjustments. Perhaps some parts of the metal need to be thickened, or a certain bending part does not need to be so sharp. These improvements will be incorporated into the design to ensure that the final product is both practical and durable.
Essentially, the prototype design and testing phase is a cycle of creation, testing, feedback, and improvement. It is a meticulous process that ensures the product has the highest quality when it begins mass production, capable of meeting the demands of the real world.
Mold Design
In the field of metal stamping, tools and molds are unsung heroes. They are the molds that shape metal forms, the tools that imprint design patterns, and the devices that ensure each stamped part is a mirror image of another. The design of these tools and molds is a process of meticulous precision, a perfect combination of engineering accuracy and craftsmanship.
Crafting specialized molds for the stamping process
The complexity of metal stamping projects often requires specialized molds. The purpose of making these molds is:
To match with materials: Different metals have different characteristics. A mold suitable for aluminum may not be suitable for stainless steel. These molds are designed with the specific characteristics of the chosen metal in mind.
To achieve complex designs: Some projects require complex designs, such as deep drawing or intricate bending. To achieve these designs, specialized molds are needed, which are often custom-made for specific projects.
To ensure safety: The design of the molds is not only precise but also safe. They ensure that there is no danger to the operators during the stamping process.Ensure Precision and Reproducibility in Production
One of the characteristics of metal stamping is the ability to produce a large number of identical workpieces. This reproducibility is achieved through carefully designed dies:
Die Design: Essentially, a die is a mold into which metal is pressed to obtain the desired shape. The design of the die determines the shape, size, and features of the stamped parts. Using advanced CAD tools, the design of the die can reach the most minute details, ensuring that each stamped part is in complete accordance with the design specifications.
Die Maintenance: Over time, dies may wear out, leading to inconsistencies in the stamped parts. Regular maintenance, including cleaning, grinding, and calibration checks, ensures that the dies remain in optimal condition, producing consistent results.
Quality Inspection: Even with the best-designed tools and dies, regular quality inspections are essential. Regularly inspecting samples from the production line according to design specifications ensures that production remains on track.
In summary, the die design phase is a combination of engineering and artistry. This phase requires precision, foresight, and a deep understanding of the stamping materials and the requirements of the final product. It lays the foundation for the mass production phase, ensuring that each product stamped is a testament to quality and craftsmanship.
Mass Production
The mass production phase is the culmination of all the careful planning, design, and prototyping. It is during this stage that the metal stamping project truly comes to life, producing one precision and high-quality product after another. However, scaling up from a few prototypes to large-scale production is not an easy task. It requires strict process control, stringent quality control, and a keen eye for detail.Upgrading from Prototype to Full Production
Transitioning from a few prototypes to thousands or even millions of mass-produced devices requires a meticulously coordinated effort:
Setup and Calibration: Press machines are equipped with carefully designed tools and dies, set up for production. This includes calibrating the machines to ensure they operate at optimal parameters for the chosen materials and designs.
Test Runs: Before commencing full-scale production, a test run is typically conducted. This involves producing a small batch of products and then subjecting them to thorough inspection to identify any discrepancies. Test runs help uncover any potential issues before they affect large-scale production.
Increasing Output: Once the test run is deemed successful, output is increased. Modern stamping machines can produce an astonishing number of products in a short period, ensuring timely delivery even for large orders.
Quality Control, Batch Testing, and Continuous Monitoring
As the machines hum and production is in full swing, the focus shifts to ensuring consistency in quality:
Quality Control: Every product on the production line reflects the project's quality standards. Regular inspections are conducted visually and with precision measuring instruments to ensure that each product meets the design specifications.
Batch Testing: While continuous checks are important, batch testing provides an additional layer of quality assurance. Samples are regularly drawn from production batches for rigorous testing, examining strength, durability, and other relevant parameters.Continuous Monitoring: Modern stamping machines are equipped with sensors and monitoring systems. These systems provide real-time feedback and alert operators when any parameters exceed the specified range. This ongoing monitoring ensures that any potential issues are identified and corrected promptly, minimizing waste and ensuring consistent quality.
Essentially, the mass production phase is a symphony of man and machine. Here, the vision of the project becomes a reality, with each stamped component bearing the mark of excellence, precision, and quality.
Finishing and Post-processing
After the metal stamping process produces the required parts, the process is not yet complete. These parts typically undergo various surface treatments and post-processing treatments to enhance their appearance, improve their durability, or add specific functional properties. This stage is crucial as it ensures that the final product not only performs its intended function but also has an excellent appearance and feel.
Surface Treatment, Painting, and Coating
While unfinished stamped metal may be functionally robust, its appearance or resistance to environmental factors may not be satisfactory. This necessitates surface treatment:
Surface Treatment: Refers to the process of altering the metal surface to achieve specific effects. For example, processes such as sandblasting or polishing can be used to smooth the surface and remove any imperfections or rough edges.
Painting: Painting serves a dual purpose. Aesthetically, it gives the stamped part its final color and appearance. Functionally, it can provide a protective layer to shield the metal from corrosion, especially for components exposed to harsh environments.
Coating: In addition to painting, metals can be coated with other materials to impart specific properties. For instance, a zinc coating can enhance corrosion resistance. Similarly, a Teflon coating can be used to provide a non-stick surface.Ensure that the final product meets aesthetic and functional requirements
The finishing and post-processing stages are guided by the requirements of the final product:
Aesthetic requirements: For components visible in the final product, aesthetics are crucial. The surface must be smooth, flawless, and consistent in color and texture. Any logos or brand elements must be clearly visible.
Functional requirements: Depending on the final use, stamping parts may need to be corrosion-resistant, high-temperature resistant, or have reduced friction. Choose post-treatment methods based on these requirements to ensure that the parts perform optimally in their intended applications.
In summary, the finishing and post-treatment stages are where the stamped metal truly transforms into a finished product. It is a fusion of art and science, ensuring that each product is not only functional but also provides visual and tactile enjoyment.
Quality assurance and delivery
The culmination of a metal stamping project is not just about producing parts, but also ensuring that each part meets the highest quality standards. Once the final polishing is complete, the focus shifts to rigorous quality assurance, followed by the logistics of delivering the finished products to customers.
Final inspection and quality check
Before any product leaves the factory, it undergoes a series of final checks:Visual Inspection: Conduct a visual inspection of each component to check for any surface defects, inconsistencies in paint or coating, and overall appearance. This ensures that aesthetic standards are maintained.
Functional Testing: Depending on the intended function of the component, specific tests may be conducted. For instance, a stamped metal part designed as a hinge may undergo tests for movement and load-bearing capacity.
Dimension Check: Use precision instruments, such as calipers and micrometers, to measure the dimensions of the components to ensure they adhere to the design specifications.
Documentation: While conducting physical inspections, also verify relevant documentation, such as certificates of conformity or material test reports. This provides additional assurance of the component's quality and compliance with standards.
Packaging, Logistics, and Delivering the Finished Product to the Customer
After quality assurance is completed, the focus shifts to getting the product into the hands of the customer:
Packaging: Carefully package the components to prevent any damage during transportation. Depending on the product and its fragility, it may be necessary to use bubble wrap, foam, or custom packaging.
Logistics: Plan the delivery logistics considering factors such as delivery deadlines, destination, and mode of transport. Whether it's by land, air, or sea, the goal is to ensure timely and safe delivery.
Communication: Maintain open communication with the customer throughout the delivery process. They will be kept informed about the shipment status, expected delivery date, and any potential delays.
Feedback and After-Sales Support: After the product is delivered, solicit feedback from the customer. This feedback is invaluable for gaining insights into any potential areas for improvement. Additionally, after-sales support ensures that the customer has a point of contact in case they encounter any queries or issues.Essentially, the "Quality Assurance and Delivery" phase is the final link in the metal stamping project. During this stage, all the hard work will be verified, the finished products will begin to be shipped to the customers, and they will be ready to meet their intended purposes at any time.
Feedback and Iteration
The completion of the metal stamping project and the delivery of the final product is not the end of the entire process. In fact, it marks the beginning of an important stage that ensures continuous improvement and refinement. This stage revolves around collecting feedback and iterating based on the insights gained.
Collecting Customer Feedback After Delivery
Once the product is in the hands of the customer, their feedback becomes invaluable:
Direct Feedback: Engage with the customers to understand their experience with the product. Are they satisfied with the quality? Does the product meet their expectations and requirements? This information can be collected through direct conversations, surveys, or feedback forms.
Performance Feedback: Beyond first impressions, understanding how the product performs in its intended application is crucial. Can it withstand the pressures it is subjected to? Are there any unexpected issues during use?
Aesthetic and Functional Feedback: While the product may be perfect in terms of functionality, customer feedback on its aesthetics, feel, and user experience can provide insights that may not have been considered during the design phase.
Continuous Improvement and Refinement for Future Projects
The insights gathered from customer feedback are invaluable for continuously improving and refining future projects. This involves analyzing the feedback to identify areas for improvement, making necessary adjustments to the design, manufacturing process, or quality control measures, and then implementing these changes to enhance the overall quality and performance of subsequent products. This iterative process ensures that each new project builds upon the lessons learned from previous ones, leading to a continuous cycle of improvement and customer satisfaction.Feedback is not just about understanding what has been done right and what has gone wrong. It's about learning and iterating:
Analyze feedback: Analyze all collected feedback to identify patterns. Are there multiple customers pointing out the same issue? Is there a certain aspect that consistently receives praise?
Implement changes: Based on the feedback analysis, implement changes in design, material selection, production processes, or other relevant aspects. This ensures that the same issues do not arise in future projects.
Share knowledge: Insights gained from one project are shared across the entire team. This ensures that everyone is on the same page, and the knowledge learned from one project benefits future projects.
Engage customers: Involving customers in the entire feedback and iteration process is crucial. This not only helps to better understand the customer's perspective but also builds trust, showing customers that their feedback is valued and acted upon.
The "feedback and iteration" phase is the pillar of continuous improvement. It ensures that each project refines processes, improves products, and strengthens relationships with customers.
Conclusion
The lifecycle of a metal stamping project demonstrates the industry's commitment to precision, quality, and customer satisfaction. By understanding each phase, we can appreciate the craftsmanship and innovation involved in transforming a sheet of metal into a functional masterpiece.
Comment