In the dynamic field of metal stamping, the service life and efficacy of parts are critical factors that determine the success of production. The frequent issues of part wear and damage not only pose a threat to production quality but also increase operational costs. However, these challenges are not insurmountable. In this article, we will explore some proven strategies and methods that can significantly reduce part wear and damage, paving the way for a more efficient and cost-effective metal stamping process.
Minimizing part wear and damage during the metal stamping process is a nuanced process that encompasses a variety of strategies. These strategies include selecting the right parts for specific applications, choosing appropriate materials and coatings for parts, implementing preventive measures, and adopting expert advice on part handling and maintenance. By employing these methods, manufacturers can greatly extend the service life of parts and ensure seamless and productive metal stamping operations.
Advertisement
We will delve into the intricacies of each strategy, providing you with a comprehensive guide that includes expert insights and practical case studies. Whether you are a seasoned professional or just starting out in the industry, this article will provide you with valuable knowledge to effectively address the challenges of part wear and damage. Therefore, please stay tuned for our approach to maintaining part integrity in metal stamping.
Understanding Part Wear and Damage
In the bustling environment of metal stamping, part wear and damage are common challenges that can disrupt smooth production. Before delving into strategies to mitigate these issues, it is essential to understand their root causes and their impacts.
Common Causes
Friction: The continuous contact between the punch and the metal sheet leads to wear, primarily due to friction. This friction gradually erodes the surface of the parts, affecting their efficiency and accuracy.
Improper Materials: Parts made from materials incompatible with the workpiece materials can accelerate wear and increase the likelihood of damage.
Lack of Lubrication: Insufficient lubrication exacerbates wear because it increases friction between the parts and the stamping materials.Overloading: Subjecting parts to loads beyond their capacity can lead to damage, affecting production schedules and increasing costs.
Impacts
Decreased product quality: Wear and damage can result in the production of substandard components, affecting the overall quality of the final product.
Increased operational costs: Frequent part replacement and maintenance can increase operational costs, affecting the profitability of the production process.
Production delays: Part failure can cause significant production delays, as the production process must be halted to replace or repair the damaged parts.
Safety concerns: Damaged parts also pose safety risks, as broken parts may cause harm to operators.
Understanding the causes and impacts of part wear and damage is the first step in developing strategies to minimize these challenges. In the following sections, we will explore various methods to ensure the longevity and efficiency of parts during the metal stamping process.
Using Parts Suitable for Your Application
In the metal stamping process, the importance of selecting the right parts for a specific application cannot be overstated to minimize part wear and damage. This crucial step not only ensures the production of high-quality components but also extends the service life of the parts. Here, we will delve into the various factors to consider when choosing the appropriate parts:
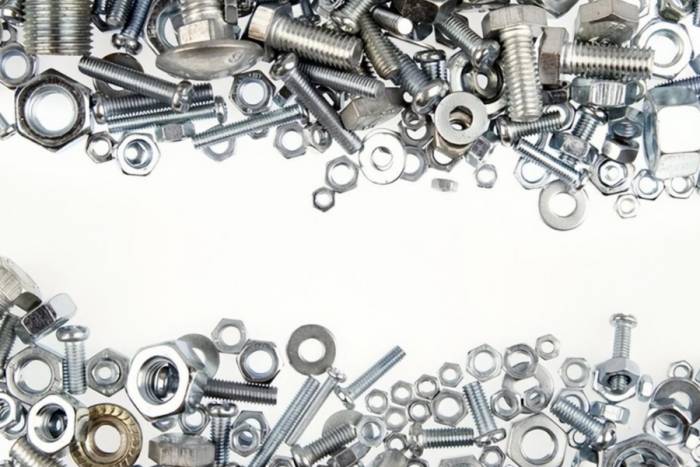
1. Material selection: The choice of material is critical, as it directly affects the durability and performance of the parts. Consider factors such as strength, hardness, and resistance to wear and corrosion.
2. Design considerations: The design of the part must be tailored to the specific application, taking into account the forces it will be subjected to, as well as the environment in which it will operate.
3. Manufacturing tolerances: Ensuring that parts are manufactured within tight tolerances is essential for proper fit and function, reducing the risk of premature wear or damage.
4. Quality control: Implementing rigorous quality control measures can help identify and address potential issues before they lead to part failure.
5. Maintenance and inspection: Regular maintenance and inspection can help detect signs of wear or damage early, allowing for timely repairs or replacements and preventing more significant issues.
By considering these factors and implementing appropriate strategies, you can minimize the risk of part wear and damage, ensuring the efficiency and reliability of your metal stamping operations.Part Types
Selecting the appropriate part types is a fundamental step in ensuring the success of the metal stamping process. Different part designs are intended to perform specific tasks, and using the wrong parts can lead to increased wear and potential damage. When choosing part types, factors such as the complexity of the task, the stamping material, and the required precision should be considered.
Punch Geometry (Shape, Size, Tolerances)
The geometry of the punch plays a crucial role in determining the quality of the stamped parts. Factors to consider include:
Shape: The shape of the punch should be consistent with the design of the part being produced. Using a punch with an inappropriate shape can lead to defects and increased part wear.
Size: Choosing the correct punch size is essential to ensure that the stamped parts meet the required specifications.
Tolerances: Maintaining strict tolerances is crucial for producing high-precision parts and preventing excessive part wear.
Part Materials and Coatings
The choice of part materials and coatings is another important consideration. Different materials have varying degrees of wear resistance, which can significantly affect the service life of the parts. Additionally, appropriate coatings can reduce friction and enhance the wear resistance and corrosion resistance of the parts. Selecting materials and coatings that are compatible with the workpiece material is essential to prevent premature wear and damage.
Die Clearance
Die clearance is the gap between the punch and the die, and it is a critical factor in the stamping process. The clearance must be carefully controlled to ensure that the parts are formed correctly and to minimize the risk of damage to the tooling. Incorrect clearance can lead to issues such as improper part formation, increased wear on the tools, and inconsistent part quality.Mold clearance, which refers to the gap between the punch and the die, is a critical factor affecting part wear. Improper mold clearance can lead to increased friction and wear, affecting the quality of stamping components. Maintaining the appropriate mold clearance is essential for ensuring a smooth stamping process and minimizing part wear and damage.
By taking these aspects into full consideration, manufacturers can significantly reduce the chances of part wear and damage, ensuring a more efficient and successful metal stamping process.
Selecting the Right Part Materials and Coatings
In the complex process of metal stamping, choosing the right part materials and coatings is the cornerstone of improving durability and reducing wear. This choice not only determines the service life of the parts but also affects the quality of the products. Here, we will explore how to select the appropriate part materials and coatings:
Understanding Different Part Materials
Different part materials possess varying degrees of hardness, toughness, and wear resistance. Here are some commonly used materials and their characteristics:
High-Speed Steel (HSS): Known for its high wear resistance and the ability to maintain hardness even at high temperatures.
Tungsten Carbide: These materials are extremely hard and have excellent wear resistance, but they may be more brittle compared to other materials.
Ceramics: These non-metallic materials offer outstanding wear resistance, especially in high-speed applications.Cobalt Alloys: These alloys are renowned for their high thermal hardness and wear resistance, making them suitable for high-temperature applications.
The Importance of Coatings
Coatings are protective layers that shield parts from adverse conditions such as corrosion and high temperatures. Here are some commonly used types of coatings and their advantages:
Titanium Nitride (TiN): A widely used coating that enhances hardness and prevents wear and corrosion.
Diamond-Like Carbon (DLC): This coating is known for its excellent wear resistance and low friction characteristics, making it suitable for high-precision applications.
Aluminum Titanium Nitride (AlTiN): A high-performance coating with outstanding heat resistance and wear resistance, particularly suitable for high-speed applications.
Making the Right Choice
Selecting the appropriate materials and coatings requires considering various factors, including the type of metal being stamped, the complexity of the stamping process, and the expected lifespan of the parts. Additionally, it is essential to work closely with material and coating suppliers to ensure that the chosen solution meets the specific requirements of the application.
By making informed choices in materials and coatings for parts, manufacturers can significantly improve the durability of parts, ensuring a smoother and more efficient metal stamping process, while reducing wear and extending the life of parts.Preventive Measures for Part Wear
In the field of metal stamping, taking preventive measures is an active approach to prevent premature part wear and ensure a seamless production process. These strategies not only extend the service life of parts but also contribute to optimizing the stamping process. In this section, we will outline various preventive strategies that help minimize part wear:
Regular Maintenance
Lubrication: Ensuring that parts are adequately lubricated can greatly reduce friction and wear. Choosing the correct type of lubricant according to the stamping material and part specifications is crucial.
Cleaning: Regularly cleaning parts helps to remove debris, preventing the accumulation of materials that cause wear and corrosion.
Inspection: Regularly inspecting parts helps to detect signs of wear early, allowing timely intervention to prevent further damage.
Optimizing Stamping Processes
Proper Part Alignment: Ensuring that parts are correctly aligned can prevent uneven wear and improve the quality of stamped components.
Temperature Management: Controlling temperatures during the stamping process can prevent adverse effects such as thermal expansion, as thermal expansion can lead to increased wear.
Control of Speed and Feed Rates: Controlling the speed and feed rates during the stamping process helps to reduce part wear, as excessive speeds can lead to increased friction and wear.Utilizing Advanced Technologies
Predictive Maintenance: Leveraging technologies such as predictive maintenance can aid in anticipating potential issues before they occur, thereby allowing for preemptive intervention measures.
Coating Technologies: Employing advanced coating technologies can enhance the wear resistance and corrosion resistance of parts, extending their service life.
Simulation and Modeling: The use of simulation and modeling technologies helps to optimize stamping processes, identifying potential issues before actual production, thus reducing the likelihood of part wear.
By implementing these preventive measures, manufacturers can create a robust framework to minimize part wear, ensuring that the metal stamping process is more efficient and cost-effective. These strategies foster a culture of preventive maintenance, which is crucial for improving the lifespan and efficiency of parts in the metal stamping industry.
Conclusion
In summary, minimizing part wear and damage during the metal stamping process is an ongoing endeavor marked by wise selection and adaptive strategies. As we have explored, choosing the right parts, appropriate materials, and coatings, coupled with preventive measures, can pave the way to success. Additionally, drawing on expert advice and industry case studies can further advance efforts in this area. Looking ahead, adopting these methods will help promote the recovery and prosperity of the metal stamping industry.
Comment