In the rapidly advancing field of electronics manufacturing, choosing the right component production method is crucial. Metal stamping is a preferred choice for many, but why is that? Let's explore the reasons behind its popularity.
Metal stamping has become favored by electronic component manufacturers because, compared to other methods, it offers shorter processing times and requires less labor.
To fully understand the advantages of metal stamping in electronic products, let's delve into its benefits and applications.
The Rise of Metal Stamping in the Electronics Industry
As the electronics industry has evolved, so have the methods for producing electronic components. Among these, metal stamping has emerged as a dominant force, offering unparalleled advantages in terms of efficiency and precision.
A Brief History
The application of metal stamping in electronic products dates back to the mid-20th century. After World War II, with the surge in demand for electronic products, manufacturers began seeking faster and more efficient ways to produce components. Metal stamping technology was thus born. Initially adopted for its speed and cost-effectiveness, it soon became apparent that stamping technology also offered extremely high precision, which is crucial for the complex parts of electronic devices. Over the decades, as technology has continued to advance, metal stamping techniques have also been refined, incorporating newer technologies and materials, ensuring its indispensable role as a tool in the field of electronics manufacturing.
Advertisement
Key Applications
The versatility of metal stamping is evident in the variety of electronic components it helps produce. Some of the main applications include:Connectors: These tiny components are responsible for connecting different parts of electronic devices, typically produced using precision stamping technology to ensure perfect fit and reliable performance.
Shielding covers: Metal stamping is used to manufacture electromagnetic shielding, protecting sensitive electronic components from interference.
Terminals: These are the endpoints of electrical connections, where precision is crucial. Stamping ensures the consistency and high quality of terminals.
Lead frames: Used for semiconductor packaging, complex designs of lead frames can be produced through advanced stamping techniques.
Heat sinks: Heat dissipation fins are key to cooling electronic devices, usually made from metal stamping with high thermal conductivity.
From everyday gadgets to advanced aerospace equipment, metal stamping plays a pivotal role in shaping the electronic products we rely on daily.
Advantages of Metal Stamping for Electronic Components
In the intricate field of electronic manufacturing, precision, speed, and cost-effectiveness are crucial. Metal stamping has proven to be a valuable asset in this domain with its unique attributes. Let's delve deeper into its specific advantages.
Speed and Efficiency
In the complex realm of electronics manufacturing, where precision, speed, and cost-effectiveness are paramount, metal stamping stands out as a valuable asset. The process offers several advantages that contribute to the efficiency and effectiveness of electronic component production.
1. High-speed production: Metal stamping allows for the rapid production of components, as the process can be automated and scaled up to meet high-volume demands. This results in faster turnaround times and increased output, which is essential for keeping up with the fast-paced nature of the electronics industry.
2. Consistent quality: The precision of metal stamping ensures that each component produced is uniform and meets strict quality standards. This consistency is crucial for the reliability and performance of electronic devices, as it minimizes the risk of defects and failures.
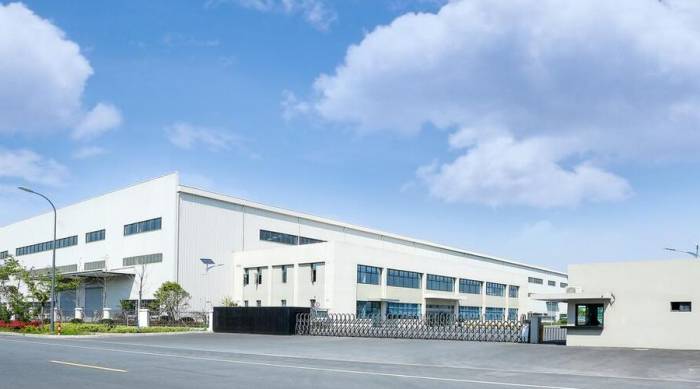
3. Cost-effectiveness: The high volume production capabilities of metal stamping, coupled with the ability to use materials efficiently, make it a cost-effective solution for manufacturing electronic components. This is particularly important in an industry where competitive pricing is key to success.
4. Customization: Metal stamping allows for the production of components with a wide range of shapes, sizes, and designs. This flexibility enables manufacturers to create customized parts that meet the specific requirements of their electronic devices, without compromising on quality or performance.
5. Material versatility: Metal stamping can be used with a variety of materials, including steel, aluminum, and copper, which are commonly used in electronic components. This versatility allows for the production of components with different properties, such as strength, conductivity, or corrosion resistance, depending on the application.
6. Environmentally friendly: Metal stamping processes can be designed to minimize waste and maximize material utilization, making it a more sustainable option for electronic component manufacturing. This is increasingly important as the industry moves towards more environmentally conscious practices.
In conclusion, metal stamping offers a range of benefits that make it an ideal choice for the production of electronic components. Its ability to deliver high-quality, cost-effective, and customized parts at a rapid pace is a testament to its importance in the electronics manufacturing sector.In an industry where time often equates to money, the rapid processing capability of metal stamping has changed the game. Traditional methods may require multiple steps and processes, but stamping can achieve the desired shape or form in just one stroke. This swift production rate is particularly beneficial to the electronics industry, as market demands are constantly changing and manufacturers need to adapt quickly. With metal stamping technology, it takes an extremely short time to produce large quantities of components, ensuring a perpetual supply shortage.
Labor Efficiency
Beyond production speed, metal stamping also significantly improves labor efficiency. The operation of automatic stamping machines requires minimal human intervention, reducing the need for a large workforce. This not only saves costs but also ensures stable production quality and avoids human errors. In an industry that demands extreme precision, this reliability is invaluable.
Precision and Consistency
Speaking of precision, metal stamping excels in producing parts with strict standards. The molds used in stamping pay meticulous attention to detail during the manufacturing process, ensuring that every part produced is consistent with the previous one. In the electronics field, even the slightest deviation can lead to functional differences, making this consistency crucial. Whether it's connectors that need to fit just right or shielding covers that must provide precise protection, metal stamping ensures that every part meets the standard every time.
Metal Stamping Compared to Other Methods
Although metal stamping has already secured a place in the electronics industry, it is also important to understand how it compares with other manufacturing methods. Let's delve into a comparative analysis.
Metal Stamping vs. Casting
Metal stamping and casting are both common methods for shaping metal, but they serve different purposes and have distinct characteristics:Craftsmanship: Metal stamping in hardware requires the use of dies and presses to shape flat metal sheets. In contrast, casting involves melting metal and pouring it into molds to solidify into the desired shape.
High Precision: Stamping is renowned for its high precision, especially suitable for thin and flat parts. Casting, while widely used for manufacturing complex shapes, may not achieve the same level of precision for certain electronic components.
Material Waste: Stamping shapes the metal directly into the required form, resulting in minimal waste. Casting, on the other hand, can lead to more material waste, particularly when the castings require further machining or finishing.
Applications in Electronics: Stamping is typically suitable for components such as connectors, terminals, and shielding covers. Casting may be more appropriate for larger, heavier parts or situations requiring specific metal alloys.
Cost Implications
When it comes to cost, several factors are at play:
Initial Setup: Metal stamping requires an investment in the design and fabrication of dies, which can be quite costly. However, once the setup is complete, the cost per part is relatively low. The cost of casting molds is also high, but the routine costs may vary depending on the complexity of the part and the type of casting method used.
Labor Costs: As mentioned earlier, metal stamping (especially automated stamping) can significantly reduce labor costs. Depending on the casting method (such as die casting versus sand casting), casting may require more manual intervention, thus incurring higher labor costs.
Material Costs: Stamping typically reduces material waste, thereby saving costs. Casting may require more raw materials, especially when post-casting processing is necessary.
Production Volume: For mass production, the per-unit cost of stamped parts is often more economical. For small batch production or specialized parts, casting may be more cost-effective.Actual Applications and Case Studies
The prominent role of metal stamping in the electronics industry is not an empty claim. Many companies have reaped tangible benefits from the application of metal stamping, and continuous innovation ensures the relevance of metal stamping in the ever-evolving technological field.
Successful Case Studies
TechGiant Inc.: TechGiant Inc. is a leading manufacturer of electronic products, and their connector product line has transitioned from traditional mechanical processing to metal stamping. What was the outcome? Production costs were reduced by 30%, and production speed was increased by 25%, effectively meeting the surging market demand.
ElectroWave Solutions: ElectroWave Solutions specializes in wireless communication equipment and uses metal stamping to produce electromagnetic shielding covers. The precision of stamping ensures the optimal performance of the equipment, leading to a 15% increase in customer satisfaction.
NanoTech Components: In the field of microelectronics, NanoTech Components leverages the precision of metal stamping to produce ultra-thin terminals for its next-generation chips. As a result, the product line has become not only more reliable but also more competitive in the market.
Innovations in the Stamping Field
The world of metal stamping is not static. As the demands of the electronics industry continue to change, stamping technology is also evolving:
High-Speed Stamping: Recent advancements have led to the development of high-speed stamping machines, which can produce components at an unprecedented rate, meeting the needs of industries with extremely high demands for product time-to-market.Precision Micro Stamping: With the miniaturization trend of electronic products, the demand for micro components is growing. Precision micro stamping technology can now produce parts as thin as a few micrometers with impeccable precision.
Hybrid Stamping: Combining traditional stamping with other processes such as forging has given birth to hybrid stamping. This method leverages the advantages of both processes, allowing for the creation of structurally more complete parts without compromising accuracy.
Intelligent Molds: Integrating sensors and artificial intelligence into stamping molds enables real-time monitoring of the stamping process. This not only ensures consistent quality but also predicts mold wear, reducing downtime and ensuring uninterrupted production.
Conclusion
Metal stamping, with its combination of speed, precision, and cost-effectiveness, has solidly become the cornerstone of the electronics manufacturing sector. From the complex connectors that power our favorite gadgets to the electromagnetic shielding that ensures optimal device performance, stamping technology plays a pivotal role in bringing technology to life.
The advantages of stamping technology are not just theoretical. As demonstrated by successful real-world cases, companies across various fields utilize the power of stamping to improve efficiency, reduce costs, and enhance product quality. With continuous innovations ranging from high-speed stamping machines to intelligent molds, the prospects for metal stamping in the electronics field are brighter than ever.
In an industry characterized by constant development and ever-increasing consumer expectations, metal stamping offers a powerful solution to these challenges. For manufacturers looking to stay ahead, leveraging the various advantages of metal stamping is not just a strategic choice but a necessity for sustained success in the dynamic world of electronics.
Comment