Understanding the quality of metal stamping parts is crucial for various industries. But how exactly should we measure it? Delve deeper to find a comprehensive answer.
The method to gauge the quality of metal stamping parts involves inspecting the precision of the stamped parts, the consistency across batches, and the presence of defects such as burrs or misalignments.
While the above provides a quick answer, there is much more to the complexity of metal stamping part quality. Let's explore further.
Understanding Metal Stamping
At the heart of metal stamping is the manufacturing process of transforming flat metal sheets into specific shapes. This is achieved by using specialized tools and dies that apply high pressure to deform and cut the metal sheet according to the desired design.
Depending on the operations involved, the process can be categorized into various types, such as punching, blanking, drawing, bending, notching, embossing, and shearing. From making holes in metal sheets (punching) to raising the metal sheet to create raised patterns (embossing), each operation serves a unique purpose.
Advertisement
Metal stamping holds significant importance across industries. It is the cornerstone of sectors like automotive, electronics, aerospace, and medical. The widespread application of metal stamping is due to its ability to produce a large number of complex parts with precision, speed, and cost-effectiveness. Whether it's the body panels of a car, connectors in electronic devices, or components in household appliances, metal stamping plays a pivotal role in bringing designs to life.
Essentially, metal stamping is not just a process but an art form that combines engineering precision with material science to produce parts that power our daily lives.Key Indicators of Quality in Metal Stamping
Ensuring the quality of metal stamping is crucial as it guarantees that the final product meets the expected specifications and performs its intended function. Here are some of the main indicators that professionals consider when evaluating the quality of metal stamping parts:
Precision of Stamped Parts
Precision is the cornerstone of the quality of metal stamping parts. Accurate stamping parts mean that every piece produced fully complies with the design specifications. Whether it is a component in a machine or a part in a large assembly, this precision ensures that the part fits perfectly with its intended application. Any deviation, even a minor one, can lead to malfunction, reduced efficiency, or even safety hazards. Therefore, significant investments are made across various industries in advanced machinery and skilled operators to achieve the highest level of precision.
Batch Consistency
While a single precision part is commendable, achieving consistency in mass production is the true guarantee of quality. Consistency ensures that every part, from the first to the last in the production process, maintains the same high standards. This consistency is crucial, especially in industries such as automotive or electronics that require thousands of identical parts. Inconsistent batches can lead to increased waste, higher costs, and potential product recalls, making consistency an important quality indicator.
Defect-Free
Defects in metal stamping parts, such as burrs, misalignment, or uneven surfaces, are clear signs of errors in the production process.
Burrs are unwanted rough edges or protrusions, usually caused by cutting operations. They can hinder the assembly process and even pose safety risks.
Misalignment refers to parts that do not conform to the design intent, leading to improper assembly.Surface irregularities may be caused by improper material handling or issues during the stamping process.
The absence of these defects is a clear indicator of quality. It signifies meticulous attention to detail, strict quality control measures, and the use of state-of-the-art machinery.
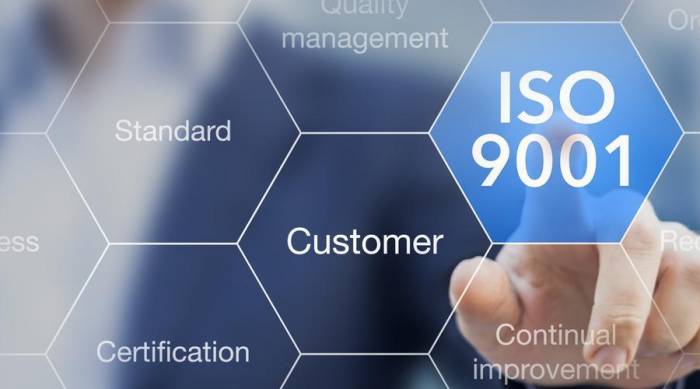
In summary, these key indicators, when closely monitored, ensure that the parts produced by the metal stamping process are not only fully functional but also reliable and safe for their intended applications.
Tools and Techniques for Measuring Quality
Ensuring the quality of metal stampings is not only about the final product but also about the processes and tools used to achieve that product. To maintain the highest standards in metal stamping, it is essential to combine advanced tools with robust quality control techniques.
Measuring Tools
Calipers: Calipers are one of the most versatile tools used for measuring the distance between two opposite faces of an object. There are various types of calipers, including vernier calipers, dial calipers, and digital calipers, each with different levels of precision.
Micrometers: Compared to calipers, micrometers offer higher precision and are used for measuring smaller dimensions. Micrometers use a screw mechanism that can measure down to thousandths of an inch or smaller.
Gages: These are specialized tools designed for specific measurement tasks. For instance, "go/no-go" gages check workpieces based on allowable tolerances, ensuring that the workpieces are neither too large nor too small. Other types of measuring instruments, such as depth gauges or ring gages, are used for specific measurement purposes.Quality Control Techniques
Statistical Process Control (SPC): This method employs statistical techniques to monitor the production process. By analyzing sample data, SPC can identify deviations from the standard process, allowing for timely corrections. It is a proactive approach to ensuring quality stability.
Visual Inspection: Sometimes, the human eye is the best tool. Trained inspectors visually examine parts for defects such as burrs, discoloration, or misalignment. Although this method may seem simple, it is often very effective, especially when combined with other techniques.
Automated Quality Checks: With technological advancements, automated systems equipped with cameras and sensors can now inspect parts at high speeds. These systems can quickly identify defects, ensuring that only high-quality parts proceed to the next stage of production.
Implementing these tools and techniques in the metal stamping process ensures that each part meets the expected quality standards, thereby reducing waste, saving costs, and ensuring customer satisfaction.
Quality's Impact on the Final Product
The quality of metal stampings is not just a metric; it is a commitment to reliability, functionality, and lifespan. When manufacturers prioritize quality, the final product benefits in multiple ways, directly affecting user experience and the entire lifecycle of the product. Here's how ensuring the quality of metal stampings impacts the final product:
Durability: High-quality metal stampings ensure that each part is manufactured to the highest standards, using the correct materials and processes. Parts produced in this manner can withstand wear and tear, environmental factors, and mechanical stress. For example, precisely stamped metal components in machinery will fit perfectly, reducing undue stress on adjacent parts, thereby extending the product's lifespan.
Functionality: The primary purpose of any product is to fulfill its intended function. Quality assurance in metal stamping ensures that each component performs its designated function accurately and reliably. For instance, precisely stamped connectors in electronic devices ensure optimal conductivity, allowing the device to operate flawlessly.Aesthetics: While the primary focus of metal stamping in hardware may be functionality and durability, aesthetics also play a crucial role, especially in consumer-facing products. High-quality stamping processes ensure clean lines, perfect fits, and a pristine finish on products. For instance, a well-stamped metal casing for a smartphone not only protects the device but also enhances its visual appeal.
Cost-effectiveness: Investing in quality may seem to increase expenses, but it saves costs in the long run. High-quality stamped parts reduce the need for replacements, repairs, and recalls. This not only saves direct costs but also preserves brand reputation, thereby maintaining customer trust and loyalty.
Safety: In industries such as automotive or aerospace, the quality of metal stampings is directly related to safety. A defect in a single part can lead to catastrophic failure. Ensuring quality means ensuring the safety of the end-users.
Environmental Impact: Quality is also connected to the environment. Products with longer lifespans reduce the need for frequent replacements. This means less waste, less resource consumption, and a smaller carbon footprint.
Conclusion
Metal stamping is a cornerstone of the manufacturing industry, playing a significant role in producing the countless parts needed for the myriad of products we use daily. The precision, durability, and functionality of these parts are directly influenced by the quality of the stamping processes. As we have explored, measuring and ensuring quality is not just a matter of compliance but a commitment to excellence, safety, and sustainable development.
From using precision measurement tools like calipers and micrometers to advanced quality control techniques such as statistical process control and automated inspection, the industry employs a multitude of methods to uphold the highest standards. These efforts not only ensure optimal performance of the final products but also enhance their lifespan, aesthetics, and safety.
Moreover, the ripple effect of quality in metal stampings extends beyond the direct product. It can save costs, reduce environmental impact, and earn the ongoing trust of consumers and stakeholders.
Essentially, the pursuit of quality in the metal stamping industry demonstrates the industry's ongoing commitment to providing the best products. It is a process of continuous improvement, innovation, and steadfast dedication to ensuring that the products we rely on, from automobiles to small tools, perform at their best.
Comment