In the intricate world of manufacturing, precision is of paramount importance. Mold service stations stand at the forefront of this precision-oriented industry, ensuring that every line, every curve, and every edge is meticulously crafted to perfection. But what exactly is a mold, and why is it so crucial?
A mold refers to the specialized tool used in the manufacturing process to cut, shape, and process materials into specific parts or products. The precision of a mold ensures the consistency, high quality of the products, and their conformity to the exact specifications required.
Delve into the nuances of molds and discover why precision is the key to achieving excellence in this field.
Who benefits most from precision mold services?
In the vast realm of manufacturing, the demand for precision is ever-increasing. As industries evolve and products become more complex, the need for exactness in every component becomes crucial. This is where precision mold services come into play, offering solutions that ensure every part is finely honed to perfection.
Precision services across industries
Advertisement
Precision mold services are not confined to a single industry. On the contrary, they span across various industries, each with its unique requirements and challenges.
Automotive: In the automotive industry, precision is critical. From engine components to intricate electronic devices, every part needs to fit perfectly to ensure the optimal performance of the vehicle. Precision mold services ensure that every component, whether it's a tiny screw or a complex gear, is manufactured to the highest standards.
Aerospace: The aerospace industry requires components that can withstand extreme conditions. Whether it's a commercial airliner or a spacecraft, its parts need to be robust, durable, and precise. Mold services play a pivotal role in ensuring that these components meet the stringent standards set by the industry.Electronic Products: As electronic devices become more compact and feature-rich, the precision required for their internal components also increases. From microchips to connectors, precision mold services ensure that these components are manufactured with the highest degree of accuracy, thereby guaranteeing the functionality and lifespan of the devices.
Consumer Goods: Even everyday items such as kitchen utensils or toys can benefit from precision mold services. These services ensure that products are safe, durable, and perform their intended functions.
Universal Solutions
Any business, regardless of its size or industry, can greatly benefit from precision mold services as long as its products require stable, high-quality parts. Whether it's a startup launching a new product or a multinational corporation expanding its production scale, precision mold services provide solutions that ensure quality, consistency, and reliability.
In summary, precision mold services are the unsung heroes of the manufacturing industry. They ensure that products across various sectors meet the highest standards, satisfying the growing demands of consumers and industries alike. As technology advances and products become increasingly complex, the role of precision mold services will only become more critical, ensuring that every production line is refined to perfection.
What Sets Your Precision Mold Services Apart in the Competition?
In an industry where precision reigns supreme, standing out in the competition requires more than just offering accurate products. It's about the entire process from the first consultation to the final product delivery. So, what exactly makes our precision mold services unique?
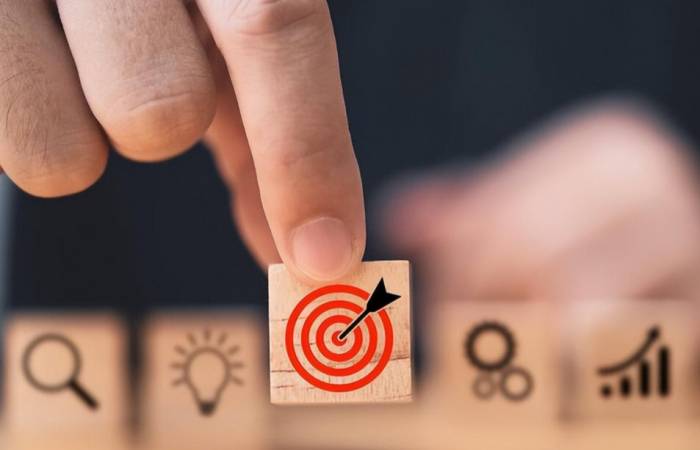
Pursuit of Excellence
Our ethos is built on a foundation of pursuing excellence. Every tool, every mold, and every component we produce is a testament to our unwavering commitment to providing the best products. Our team, from craftsmen to engineers, has been trained to the highest standards, ensuring that every product that leaves our factory is flawless.Continuous Innovation
While we take pride in our traditional craftsmanship, we are not bound by it. We believe in embracing the future, which means continuous innovation. By investing in the latest technologies and machinery, we ensure that our production processes are not only efficient but also at the forefront of the industry. This fusion of tradition and technology allows us to produce molds that are both high-quality and advanced.
Customer-Centric Approach
We understand that each customer is unique, with specific needs and challenges. Therefore, we adopt a customer-centric approach, listening, understanding, and then delivering. From personalized consultations to tailored solutions, we ensure that our services perfectly match the individual needs of every client. Our professional customer support team is always on standby to promptly address any queries, concerns, or feedback.
Quality Control
Quality is more than just a slogan for us; it's a way of life. We have stringent quality control measures to ensure that every product undergoes rigorous testing and inspection. Our quality assurance team ensures that every set of molds meets industry standards and our own internal benchmarks.
Customized Solutions
We recognize that off-the-shelf solutions do not always fit the bill. Therefore, we offer customized solutions, tailored to meet the unique needs of each client. Whether it's specific materials, unique designs, or challenging deadlines, we can handle it all, providing you with a tailored solution.
In a market crowded with competitors, our precision mold services stand out, not only for the products we offer but also for the experience we provide. Our pursuit of excellence, courage to innovate, and customer-centric focus set us apart. By choosing us, you get more than just a product; you get a commitment to quality, precision, and unparalleled service.What materials and technologies are used in precision mold manufacturing?
Precision mold manufacturing is a complex process that requires the combination of the right materials and advanced technologies to produce parts that meet strict standards. Let's delve into the materials and technologies that determine our precision mold manufacturing processes.
Materials used:
Tool steel: Such as SKD11 and D2, these steels are widely used in mold manufacturing due to their strength and wear resistance.
High-Speed Steel (HSS): HSS is appreciated for its ability to maintain hardness at high temperatures and is often used to manufacture tools that require long-lasting durability and wear resistance, such as cutting tools and drill bits.
Cemented carbide (tungsten steel): This is an alloy primarily composed of tungsten and carbon. Its significant hardness and durability make it the preferred material for manufacturing tools that need to maintain sharpness over long periods.
Various alloys: Depending on the specific requirements of the mold, we select various alloys to ensure the optimal combination of strength, durability, and corrosion resistance. These custom alloys provide the specific performance needed to ensure that every final product meets the predetermined specifications.
Technological applications:
Wire Electrical Discharge Machining (WEDM):
Wire Electrical Discharge Machining is a machining technology that cuts materials through electrical sparks generated by pulsed currents. It uses a thin wire as an electrode, and the cutting is achieved by the erosion of the workpiece material through the generated electrical sparks. This method is particularly suitable for high-hardness, difficult-to-machine materials such as cemented carbide and high-speed steel. Its main advantages include:Capable of processing complex, delicate, and fragile shapes.
Does not generate mechanical stress on the workpiece.
High precision, achievable to ±0.002mm.
Oil-cutting processing (Oil-Type WEDM):
Oil-cutting processing is a specific version of wire electrical discharge machining (WEDM), which uses special oil as the working fluid instead of the usual deionized water. Compared to the traditional water-based WEDM, using oil as the medium can better control the spark process, thereby providing a more accurate and smoother cutting surface. In addition, the use of oil also reduces the risk of wire electrode breakage and helps to improve machining accuracy and surface quality.
Machining accuracy can reach ±0.002mm or better
Under ideal operating conditions, its Ra value (a standard measure of surface roughness) can reach 0.1μm or lower
It can achieve high precision and superior surface quality on high-hardness, difficult-to-machine, or sensitive materials
Optical grinding processing (PG):
Optical grinding processing, also known as Profile Grinding, is a high-precision grinding technique that uses a grinding wheel. It is widely used in the manufacturing of high-precision components such as molds, mold parts, and precision bearings. The main features include:High Precision: Capable of achieving micron-level accuracy.
Good surface finish: Can achieve Ra0.1μm.
Can process various materials, including hardened steel and hard alloys.
Coordinate grinding (JG) processing:
Coordinate grinding is performed using a precision coordinate grinding machine. This machine features a highly accurate CNC system and a high rigidity structure, enabling extremely high machining accuracy. It is commonly used for the processing of precision molds, parts, and other workpieces that require a high degree of precision. Its characteristics include:
High machining accuracy, which can reach 0.001mm.
Suitable for complex workpiece shapes.
High degree of automation, reducing the possibility of manual intervention.
Precision mold manufacturing is the combination of selecting the right materials and adopting the best techniques. By combining traditional methods with modern approaches, we ensure that every product we produce meets the highest quality and precision standards. Whether it is a simple tool or a complex mold, we are committed to using the best materials and techniques to ensure that our customers receive products that exceed their expectations.Why is precision crucial in mold manufacturing?
In the intricate field of mold manufacturing, precision is not just a desirable trait but an absolute necessity. The importance of precision in this domain cannot be overstated for the following reasons:
Consistency: Precision ensures that every set of molds produced is consistent with the previous set. This consistency is vital, especially in mass manufacturing where thousands or even millions of parts are produced. Any inconsistency can lead to variations in the final product, affecting its functionality and quality.
Reduction of waste: Imprecision in mold manufacturing can lead to significant material waste. If molds are not precise, they may not fit or function correctly, rendering them ineffective. This not only results in material waste but also increases production costs. Precision ensures that every product manufactured meets the standards, minimizing waste and increasing efficiency.
Guarantee of specifications: Molds are typically manufactured according to specific customer or industry specifications. Precision ensures that these specifications are met accurately. Whether it's specific dimensions, shapes, or functions, precision guarantees that the molds perfectly align with the required specifications.
Crucial for sensitive industries: Certain industries, such as aerospace, medical, and automotive, have extremely stringent standards. In these industries, even minor deviations can have serious consequences. For instance, imprecise tools used in aircraft parts or medical equipment can jeopardize safety. In these sectors, precision is non-negotiable and of paramount importance.
Enhancement of product quality: The precision of mold manufacturing directly impacts the quality of the final product. Precisely manufactured tools will produce high-quality parts, thereby enhancing the overall quality of the final product. This not only meets customer expectations but also strengthens the brand's reputation for quality and reliability.
Cost-effectiveness: Although achieving precision may require initial investments in technology and training, it pays off in the long run. Precise molds reduce the need for rework, minimize waste, and ensure efficient production processes. This leads to cost savings and increased profit margins.
In mold manufacturing, precision is the cornerstone of success. It ensures consistency, quality, and efficiency, making it indispensable. In some industries, even a micron can make a difference, so the importance of precision cannot be emphasized enough. It is not just about meeting specification requirements but also upholding a commitment to excellence, safety, and reliability.Conclusion
The precision of molds is not just a requirement; it is an art form. It represents a delicate balance between craftsmanship and technology, tradition and innovation. As the industry continues to evolve, our commitment to precision for every production line remains unwavering. Whether you are a business seeking reliable mold services or an individual curious about the industry, remember—precision is the key to excellence.
Comment