In the ever-evolving manufacturing industry, the metal stamping process stands as a beacon of efficiency and precision. In this article, we will delve into the various stages of the metal stamping manufacturing process, revealing the nuances of this critical procedure in modern manufacturing.
The metal stamping manufacturing process is a comprehensive procedure that involves a series of stages such as engineering design, die development, raw material procurement, processing, die assembly, trial runs, first inspection, trial production, mass production, quality inspection, packaging, and delivery. Characterized by advanced technology and professional execution, this process ensures accuracy and optimal material utilization.
Let us explore each stage of the metal stamping manufacturing process to gain an in-depth understanding of the specialized techniques and experiences within this industry.
Process Flow
In the manufacturing realm, the metal stamping process is renowned for its precision and high efficiency, playing a pivotal role. This process consists of a series of meticulously arranged steps that transform concepts into tangible products.
Let's delve into the complexity of each stage:
Engineering Design: Blueprint for Success
Advertisement
At the inception of the metal stamping manufacturing process, we find the engineering design phase, where meticulous planning and design are required. During this phase, experts consider various factors such as material properties, design complexity, and production feasibility to draft the product blueprint. This phase is fundamental, ensuring that subsequent processes are streamlined and successful.
Die Development: Meticulous Craftsmanship
In the next phase, die development takes center stage. This is where the precision and intricacy of the metal stamping process are finely honed. Engineers and technicians work closely to design and manufacture the dies that will shape the metal into the desired form. The dies must be designed to withstand the high pressures and repeated use, ensuring that the final product meets the exact specifications.
Raw Material Procurement: Selecting the Best
The selection of raw materials is a critical aspect of the metal stamping process. The quality and type of metal used can significantly impact the final product's performance and durability. Suppliers are carefully chosen based on the quality of their materials, reliability, and cost-effectiveness.
Processing: Shaping the Future
Once the dies are ready and the raw materials are procured, the actual processing begins. This involves the use of stamping presses to shape the metal according to the die's design. The process requires precise control over the machinery to ensure that each part is formed correctly and consistently.
Die Assembly: Setting the Stage
Before the trial runs can begin, the dies must be assembled correctly. This involves setting up the press and ensuring that all components are aligned and secure. Proper die assembly is crucial for the success of the stamping process, as any misalignment can lead to defects in the final product.
Trial Runs: Testing the Waters
Trial runs are conducted to test the effectiveness of the dies and the processing parameters. These runs help identify any issues with the design or the process, allowing for adjustments to be made before full-scale production begins.
First Inspection: Quality at the Forefront
After the trial runs, the first inspection is conducted to ensure that the parts produced meet the required quality standards. This inspection involves a thorough examination of the parts for any defects or inconsistencies.
Trial Production: Refining the Process
Following the successful first inspection, trial production begins. This phase is a scaled-up version of the trial runs, allowing for further refinement of the process and the identification of any remaining issues.
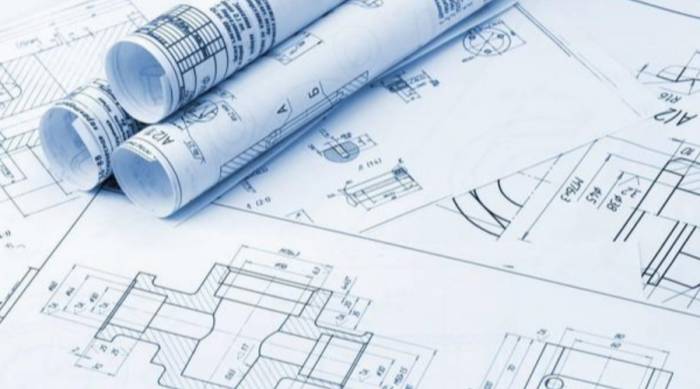
Mass Production: Scaling Up
Once the process has been refined and all issues have been addressed, mass production commences. This is where the efficiency of the metal stamping process truly shines, as it allows for the rapid and consistent production of high-quality parts.
Quality Inspection: Ensuring Excellence
Throughout the production process, quality inspections are conducted to ensure that the parts meet the required standards. This involves rigorous testing and inspection to catch any defects that may have been missed earlier in the process.
Packaging and Delivery: Wrapping Up
The final stages of the metal stamping manufacturing process involve packaging the finished parts and preparing them for delivery. This includes ensuring that the parts are protected during transit and that they arrive at their destination in perfect condition.
By understanding each stage of the metal stamping manufacturing process, we can appreciate the complexity and precision that goes into creating high-quality metal components that are essential to a wide range of industries.After the completion of the engineering design phase, the focus shifts to mold development. This stage involves the creation of basic tools and molds that facilitate the manufacturing process. Experts in this field strive to develop molds that are both efficient and precise, laying the foundation for a smooth manufacturing process.
Raw Material Procurement: Pursuit of Quality
The next step in the process is raw material procurement, a critical phase for identifying and sourcing the correct materials that form the backbone of the process. This stage ensures that the selected materials are of high quality and suitable for the specific requirements of the product, paving the way for successful manufacturing.
Mold Manufacturing: Optimal Precision
As time progresses, we enter the mold manufacturing phase. During this phase, the molds developed earlier are manufactured with the highest precision. This stage is characterized by meticulous attention to detail, ensuring that each set of molds meets the strict standards set in the manufacturing process.
Mold Assembly: Setting the Stage
Mold assembly is a continuation of the entire process, where the carefully crafted molds are assembled to lay the groundwork for production. This stage ensures that all components are perfectly aligned, preparing for a seamless production process.
Trial Molding: Ensuring Functionality
Before moving into full-scale production, trial molding is a central phase. In this stage, the assembled tools are tested to ensure their functionality and efficiency. The trial run helps to identify any potential issues so that adjustments can be made before commencing mass production.
First Inspection: Meeting Standards
The first inspection is a crucial step to ensure that the products meet the required standards. This stage involves a thorough examination of the initial production batch to confirm that they adhere to the specifications and quality benchmarks set forth for the product.After the trial molding, the first article inspection will be conducted. This is a crucial examination to ensure that the first product produced meets the established standards. It serves as a quality checkpoint to ensure that the product meets the expectations and specifications set forth during the engineering design phase.
Pilot Production: Testing the Waters
Before commencing mass production, a preliminary production run, known as pilot production, is carried out. This phase tests the efficiency of the process to make necessary adjustments and ensure a smooth transition to mass production.
Mass Production: Scaling Up
As the final phase approaches, large-scale production begins. During this stage, production is carried out on a large scale according to specified quality standards. This phase is characterized by efficiency and precision, ensuring that each product meets the expected quality benchmarks.
Quality Inspection: Striving for Excellence
After mass production, a rigorous quality inspection is conducted. This phase ensures that the products meet quality benchmarks and adheres to the excellence standards of metal stamping manufacturing processes.
Packaging: Ensuring Product Safety
Towards the end, the packaging phase begins. During this stage, products are properly packaged for delivery. This phase ensures that the packaging of each product prevents damage during transportation and maintains the quality achieved during the production process.
Delivery: The Final Milestone
This marks the final stage where the products are delivered to the customers, signifying the successful completion of the production and distribution process.Finally, we arrive at the delivery phase, the last milestone in the metal stamping manufacturing process. Here, products are shipped to their respective destinations, ready to be integrated into various applications, marking the successful conclusion of the manufacturing journey.
Our Definition
In the dynamic field of metal stamping manufacturing, certain factors determine the professionalism and success of the industry. Let's explore these decisive factors:
Technology + Experience = Expertise
In the metal stamping industry, the perfect combination of cutting-edge technology and extensive experience creates unparalleled expertise. This synergy ensures that products are not only of superior quality but also reflect innovation and professionalism. Through years of honing skills and adopting the latest technological advancements, professionals in this field can provide solutions that meet and exceed industry standards.
Accuracy in Best Practices
Precision is the cornerstone of the metal stamping process. It is achieved through meticulous planning and execution at every stage of the manufacturing process. From the initial design phase to the final product delivery, ensuring accuracy is a deeply ingrained philosophy within the industry. This commitment to precision results in reliable products that can meet the exact specifications demanded by clients.
Selecting the Right Components
The success of a metal stamping project often hinges on selecting the right components. This requires a deep understanding of the project requirements and a careful evaluation of the various components available. By choosing the right components, manufacturers can ensure a smoother production process and a final product that meets the expected quality and functionality. This guide serves as a beacon, helping professionals navigate the selection process with ease, ensuring the right choices are made at every critical juncture.Material Utilization Rate Affects Cost
In the process of metal stamping, the material utilization rate plays a significant role in determining overall costs. Effective material utilization not only helps to reduce waste but also helps to control costs. By maximizing the material utilization rate and minimizing waste, manufacturers can strike a balance between quality and cost-effectiveness. This discussion reveals the various strategies that industry professionals adopt to optimize material utilization, ultimately having a positive impact on the cost structure.
Assembly and Packaging
As we approach the pinnacle of the metal stamping manufacturing process, two key stages come into play: assembly and packaging. These two stages are crucial for ensuring that the product not only meets quality standards but also arrives at the customer safely and intact. Let's delve deeper into these final yet critical stages:
Assembly: The Perfect Harmony of Components
During the assembly stage, all meticulously crafted parts come together to form the final product. This process is characterized by precision and professionalism, ensuring that each component fits perfectly with the others. Here, the product begins to take its final shape, reflecting the quality and excellence of metal stamping manufacturing. The assembly process fully embodies the harmony between the parts, creating a product that meets the highest standards of quality and functionality.
Packaging: Ensuring Quality and Safe Delivery
Once the assembly process is complete, the focus shifts to packaging. This stage is not just about putting the product into a box; it includes a series of steps to ensure that the product is properly protected and ready for delivery. The packaging process takes into account factors such as the product's size, weight, and fragility, and employs various measures to ensure quality and safety during transportation. The packaging reveals the meticulous efforts made to protect the product, ensuring that it reaches the customer in perfect condition, fulfilling its intended purpose.
ConclusionAs we traverse the intricate journey of metal stamping manufacturing, it becomes evident that each phase plays a pivotal role in crafting products that embody quality and precision. From the initial planning and engineering design to the final assembly and packaging, every step reflects the industry's commitment to excellence and innovation.
The synergy of technology and experience, emphasis on accuracy, and meticulous selection of components and materials all contribute to achieving an efficient and reliable process. Moreover, the focus on sustainable material utilization also indicates that the industry is not only dedicated to creating outstanding products but also to fostering a greener manufacturing environment.
In summary, the metal stamping manufacturing process is a beacon of professionalism, where technical expertise and innovation merge to produce reliable and highest-quality products. In this process, meticulous planning and execution are combined to carefully craft solutions that meet the dynamic needs of various industries.
Comment