Deep drawing is a cornerstone of the manufacturing industry, revolutionizing the way we produce complex metal components. As industry evolves, the significance of this technology grows, making it imperative for professionals and enthusiasts alike to grasp its nuances. Did you know that over 40% of all metal products we use daily are manufactured through the deep drawing stamping process, highlighting its widespread applicability and efficiency?
Deep drawing stamping is a metal forming process that uses a series of dies to radially draw a metal sheet blank into a forming die, creating a three-dimensional shape. This technique is particularly suited for producing complex, high-precision metal parts where other methods might struggle.
Eager to delve deeper? Join us as we unveil the mysteries of deep drawing, introduce you to the processes and advantages of deep drawing, and answer the hottest questions surrounding this critical manufacturing method.
What is deep drawing stamping?
Deep drawing stamping is a specialized metal forming process that transforms a flat metal sheet (commonly referred to as a blank) into a deep, hollow shape, or what is known as a "drawn" part. Standard stamping typically shapes metal without significantly altering its depth, whereas deep drawing stamping focuses on creating parts with a depth greater than their diameter.
Advertisement
Process Flow
Starting with the blank: The process begins with a flat sheet of metal, selected based on the specifications of the final product desired.
Drawing the metal: A stamping press forces the metal sheet into the die cavity, shaping the metal into the required form. This may be done in several stages, with each stage drawing the metal deeper, bringing it closer to its final shape.
Redrawing: For particularly deep parts, the metal can be redrawn through a series of dies, progressively forming it without compromising its integrity.Common Materials
Deep drawing stamping is widely used and can be performed on a variety of metals. The most commonly used materials include:
Stainless steel: Known for its corrosion resistance and strength.
Aluminum: Lightweight and highly ductile, making it an ideal material for complex shapes.
Carbon steel: Offers a balance of durability and malleability.
Copper: Renowned for its excellent electrical conductivity, often used in electrical components.
Brass: Frequently chosen for its aesthetic appeal and corrosion resistance.
The choice of material typically depends on the intended use of the finished product, as each metal has its unique properties that may offer advantages in specific situations.
Advantages of Deep Drawing StampingDeep drawing stamping, while a technical process, boasts numerous advantages and is the preferred choice for many manufacturers. Here are some of its standout benefits:
Cost-effectiveness: One of the most striking advantages of deep drawing stamping is its cost-effectiveness. By using a series of progressive dies in a single operation, manufacturers can quickly produce large quantities of parts, reducing labor costs and waste. Over time, this can lead to significant cost savings, especially when producing large volume orders.
Versatility in producing various shapes: Deep drawing is not limited to simple or standard shapes. Its process allows for the creation of complex, intricate designs that may be challenging or even impossible to achieve with other methods. Whether your goal is cylindrical, conical, rectangular, or any other unique shape, deep drawing stamping technology can meet your needs.
High-quality surface finish: The nature of the deep drawing stamping process ensures that the finished parts have a smooth, high-quality surface finish. The metal is stretched and compressed, not cut or joined, which means there are no seams, rough edges, or irregularities. This not only enhances the aesthetic appeal of the product but also ensures its durability and functionality.
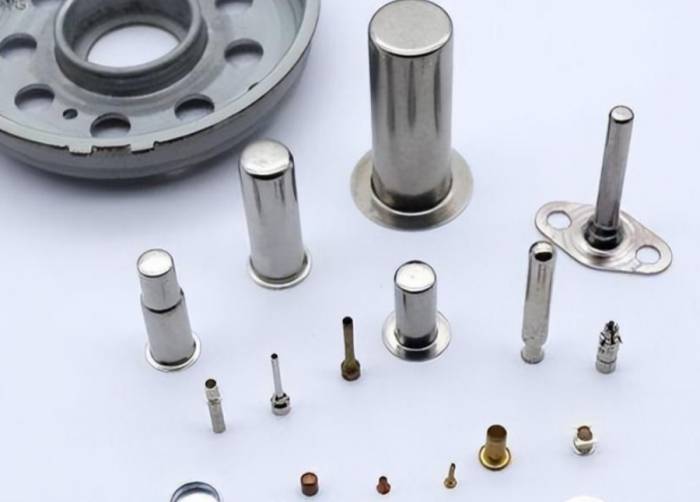
Incorporating deep drawing technology into the manufacturing process can produce high-quality products, reduce production costs, and give a competitive edge over rivals who still rely on more traditional, less efficient methods.
Common applications of deep drawing:
Deep drawing stamping has the capability to produce complex and durable parts, applicable in multiple industries. Its versatility and efficiency make it the preferred method for meeting a variety of manufacturing needs.
Industries that frequently use this method include:
Automotive industry: Deep drawing stamping plays a pivotal role in the production of parts such as fuel tanks, mufflers, and various engine components.Aerospace Industry: Aircraft shells, engine components, and other critical parts are often produced using this method due to their precision and durability.
Medical: Surgical instruments, medical device casings, and implantable parts typically rely on deep drawing because of its high precision and compatibility with biocompatible metals.
Electronics: Battery casings, metal casings for electronic devices, and connectors are all application areas of deep drawing technology.
Household Appliances: From cookware to washing machine drums, many household items benefit from the deep drawing stamping process.
Examples of products manufactured using the deep drawing stamping process:
Beverage Cans: The cylindrical and smooth surfaces of beverage cans are achieved through the deep drawing stamping process.
Cooking Pans: The deep seamless structure of many cooking pans is the result of this method.
Fire Extinguisher Shells: The robust and durable seamless shells of fire extinguishers are usually manufactured using the deep drawing stamping process.
Camera Metal Housings: Protective metal housings for many cameras and photographic equipment are made using this process.
Spray Cans: The familiar shape and design of spray cans are the direct result of deep drawing stamping.The extensive application of deep drawing stamping technology across various industries has demonstrated its efficiency, versatility, and consistent high quality.
Challenges in Deep Drawing Stamping
Although deep drawing stamping offers numerous advantages, like other manufacturing processes, it also faces a range of challenges. Recognizing these challenges and implementing effective solutions is crucial for maintaining efficiency and product quality.
Potential Issues During the Processing
Wrinkling: When the metal sheet is drawn into the die, it may wrinkle, especially in the flange area.
Tearing: If the metal is stretched too thin during the drawing process, tearing can occur.
Springback: After the metal is formed, it may attempt to return to its original shape, leading to inaccurate dimensions.
Surface Defects: Scratches, marks, or blemishes may appear if the metal sheet comes into unnecessary contact with other surfaces.
Material Variations: Differences in material properties can lead to inconsistencies in the final product.Solutions and Best Practices for Overcoming These Challenges
Optimizing die design: A well-designed die can minimize wrinkling and tearing. It is essential to ensure that die radii and blank holding forces are optimized.
Lubrication: Proper lubrication can reduce friction, prevent surface defects, and ensure a smoother drawing process.
Material selection: Choosing the right material with consistent performance is crucial. Pre-testing the material's consistency helps achieve uniform results.
Slowing down the drawing speed: Reducing the drawing speed can help prevent tearing, especially for metals with higher ductility.
Post-processing treatments: Processes such as annealing can help reduce the effects of springback and ensure the metal maintains the desired shape.
By understanding these challenges and implementing the suggested solutions, manufacturers can ensure that the deep drawing stamping process is as efficient and error-free as possible.
Comparison of Deep Drawing Stamping with Other Stamping Methods
Stamping is a broad category of metal forming, and deep drawing stamping is one of its specialized branches. When comparing deep drawing stamping with other stamping methods, it is necessary to understand its unique advantages and potential drawbacks.Advantages of Deep Drawing Stamping
Complex Shapes: Deep drawing stamping excels at producing intricate, deep, and complex shapes, which can be challenging for other methods.
High Material Efficiency: This method typically reduces waste since the metal is stretched into shape rather than being cut away.
Seamless Components: The resulting parts are seamless, enhancing their strength and aesthetic appeal.
Consistency: With proper setup, deep drawing stamping can produce a large quantity of consistent, high-quality parts.
Disadvantages of Deep Drawing Stamping
Initial Setup Costs: The process requires specialized dies, and the initial production costs can be high.
Material Limitations: Not all metals are suitable for deep drawing stamping, which limits the range of materials that can be used.
Depth Limitations: Although deep drawing is well-suited for manufacturing deep parts, there are limits to the depth of the drawn parts without introducing defects.
When to Choose Deep Drawing Over Other MethodsDeep Drawing Stamping: A Preferred Choice for Certain Applications
When the depth required for a part exceeds half of its diameter, deep drawing stamping is often the method of choice. This process is particularly suitable for creating parts with a deep, uniform shape that would be difficult or impossible to achieve with other stamping techniques.
Material Efficiency: For projects where material conservation is a priority, deep drawing stamping stands out for its efficiency in reducing waste. The process allows for the creation of parts with minimal material usage, thus saving costs and resources.
Seamless Construction: If the end product requires a seamless structure, such as certain containers or cylinders, deep drawing stamping technology is the optimal choice. The seamless nature of the parts produced by this method ensures strength and integrity, which are crucial for applications where leaks or breaks are not acceptable.
Mass Production: For large-scale production with high consistency requirements, the repeatability of deep drawing stamping is a significant advantage. This method allows for the production of uniform parts in large quantities, which is essential for industries that demand precision and uniformity in their products.
In conclusion, while deep drawing stamping has many advantages, it is essential to evaluate the specific requirements of a project to determine if it is the most appropriate method or if other stamping techniques might be more suitable.
Deep drawing stamping is a testament to the evolution of manufacturing processes, combining efficiency, precision, and versatility. Its ability to produce complex, seamless parts has made it an indispensable tool across various industries, from automotive to electronics. As we delve deeper into its nuances, advantages, and applications, the significance of this method becomes strikingly clear. It not only shapes the products we use daily but also the trajectory of the future development of the entire manufacturing industry.
Looking ahead, one cannot help but ponder: How will deep drawing technology evolve over the next decade with the rapid advancements in technology and material science? In our ever-evolving world, what role will deep drawing stamping play in shaping the next generation of products?
Comment