In the fiercely competitive manufacturing industry, the emergence of progressive stamping technology has changed the game. But how exactly does it improve speed and reduce costs? Let's find out.
Progressive stamping facilitates production by simplifying operations, ensuring precision, and reducing waste, thereby significantly lowering costs.
To fully understand the impact of progressive die stamping in the manufacturing industry, let's delve into its complexities.
Understanding Progressive Die Stamping
In the vast world of manufacturing, precision and efficiency are paramount, and progressive die stamping technology has secured its place among them. Although not a new method, it has been refined over the years to meet the evolving needs of industries ranging from automotive to electronics.
The Core of Progressive Die Stamping
The essence of continuous stamping is a metalworking method that utilizes a series of stamping stations. Each station performs a unique operation on the metal sheet, and as the sheet progresses through the stations, it transforms into a finished part. This continuous feed process is the origin of the name progressive die stamping.
Advertisement
The advantage of this method lies in its ability to produce complex parts at high speeds. Imagine a meticulously coordinated assembly line designed for metal parts. Each station in the stamping process is carefully designed to ensure that the metal is shaped, cut, or bent into a specific form. By the time the metal sheet reaches the end of the line, it has been transformed into a component ready for assembly or sale.
The Step-by-Step Mechanical Principle
The progressive die stamping process involves a series of steps that are meticulously orchestrated to achieve the desired outcome. Each station in the process is responsible for a specific task, such as punching, bending, or forming the metal. The precision of these operations is crucial, as any deviation can lead to defects in the final product.
1. **Feeding**: The process begins with the feeding of the metal sheet into the die. This is often done automatically to ensure consistent and accurate placement.
2. **Piercing**: The first station often involves piercing the metal to create holes or cutouts. This is done with precision tools that are designed to minimize material waste.
3. **Bending**: Subsequent stations may involve bending the metal into the desired shape. This is achieved through the application of controlled force and pressure.
4. **Forming**: Some parts may require forming, where the metal is shaped into a specific contour. This is done with dies that are designed to match the final part's profile.
5. **Trimming**: After the part has taken its final shape, any excess material is trimmed away. This ensures that the part is ready for assembly or further processing.
6. **Ejecting**: The final step is to eject the finished part from the die. This is often done with a mechanical or pneumatic system that pushes the part out of the die and onto a collection conveyor.
The entire process is highly automated and can be controlled by computer systems to ensure consistency and efficiency. The use of progressive dies allows for the production of complex parts in a single pass, reducing the need for multiple setups and operations, which in turn lowers production costs and increases throughput.
In conclusion, progressive die stamping is a highly efficient and cost-effective method for producing a wide range of metal parts. Its ability to automate complex processes and ensure precision has made it an indispensable technology in the manufacturing industry.Let's break down a typical progressive stamping operation:
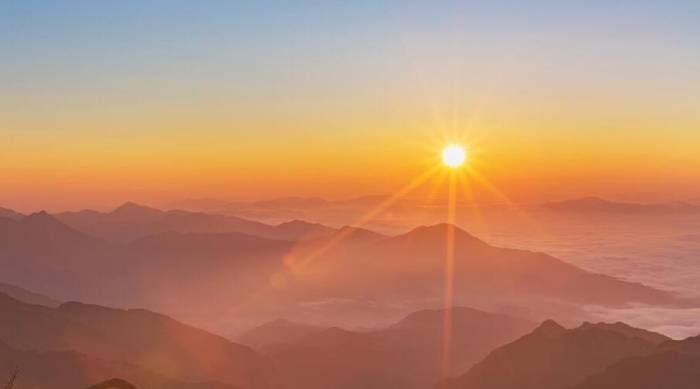
Feeding: The metal coil is fed into the stamping press. As the process progresses, the metal coil gradually unrolls.
Guiding: As the metal moves forward, guide pins are used to align it, ensuring the precision of subsequent operations.
Stamping: The metal strip then reaches the stamping station. Here, custom-designed dies are used to perform various operations on the metal strip, such as bending, punching, extruding, and embossing.
Progression: After each stamping action, the metal sheet advances a certain distance, which is known as "progression." This ensures that the next part of the metal strip aligns perfectly with the subsequent station.
Trimming and Shaping: As the metal sheet moves between stations, excess material is trimmed to form the required shape.
Drop-off: Once the part is fully formed, it is separated from the scrap and ejected from the stamping press.
Collection: The finished parts are then collected, ready for further processing or assembly.
This streamlined process ensures that multiple parts are produced with each press stroke, maximizing efficiency and output.Interpreting the Advantages
Progressive die stamping, despite its complex process, boasts numerous advantages and is the preferred choice for many manufacturers. From its rapid production pace to impeccable precision, let's delve into the strengths that have solidified its position in the manufacturing sector.
Speed and Efficiency
A standout feature of progressive die stamping is its ability to produce parts at an astonishing speed. Due to the continuous feeding characteristic of this process, multiple parts can be manufactured with each stamping stroke. This means that once set up, the stamping press can produce thousands of parts per hour, depending on the complexity of the design.
Moreover, the efficiency of this method is not just about speed. The simultaneous operation of multiple stamping stations means that a single stamping can accomplish what other methods might require several processes to complete. This combined operation shortens the time from raw material to finished product, thereby simplifying the entire production process.
Precision and Consistency
In an industry where a deviation of a single millimeter can lead to product failure, the precision of progressive die stamping is a godsend. Custom-designed dies ensure that each part produced is identical to the last, strictly adhering to design specifications. This consistency is crucial, especially when producing parts for industries such as aerospace or medical devices, where consistency is non-negotiable.
Furthermore, the automated nature of this process minimizes human intervention, reducing the potential for errors that may arise from manual operations. This automation ensures that the quality remains consistent, whether it's the first part or the ten thousandth zero.
Economic Advantages
From an economic perspective, progressive die stamping technology offers several advantages. The initial setup, while potentially more costly due to custom dies, is worth it in the long run. Once established, the cost per part is significantly reduced, especially during mass production.This method can minimize waste to the greatest extent and also helps to improve cost-effectiveness. By effectively utilizing metal strip and reducing waste, manufacturers can maximize the use of raw materials. Moreover, due to the reduced demand for labor, coupled with the fast production speed, this means that the total cost of producing each part is lower than many other methods.
Material and Design Aspects
Progressive die stamping, although versatile, requires careful consideration of materials and design to ensure the best results. The choice of metal and the complexity of the design play a crucial role in determining the success of the stamping process. Let's explore these aspects in detail.
Optimal Stamping Materials
The choice of material is crucial in progressive die stamping as it directly affects the quality of the finished product. Here are some commonly used metals and their characteristics:
Steel and Stainless Steel: These are the most commonly used materials due to their strength and durability. Stainless steel, because of its corrosion resistance, is particularly popular for parts that need to be used in harsh environments.
Aluminum: Lightweight and easy to form, aluminum is an ideal choice for parts that require a balance of strength and weight. Its natural rust resistance makes it a preferred choice for automotive and aerospace applications.
Copper: Known for its excellent electrical conductivity, copper is often used in electrical components. Its formability makes it suitable for complex designs.
Brass: This alloy composed of copper and zinc is renowned for its corrosion resistance and is commonly used in plumbing parts and decorative items.Titanium: With a high strength-to-weight ratio, titanium is used in industries such as aerospace where strength without adding weight is crucial. It is worth noting that the choice of material also depends on the intended use of the part, the environment it will be exposed to, and budget considerations.
Design Flexibility and Limitations
Progressive stamping offers a wide range of design possibilities but also has inherent limitations:
Flexibility:
Complex shapes: Progressive die stamping can produce parts with complex designs, including parts with bending, extrusion, and embossing.
Tight tolerances: This method can achieve tight tolerances, ensuring that parts fit perfectly within assemblies.
Limitations:
Material thickness: There are limitations on the thickness of the metal sheets that can be stamped. Extremely thick materials may require alternative methods.
Deep drawing: Although stamping can handle drawn parts, the depth of drawing is limited. Extremely deep drawing can be challenging.Mold Cost: The cost of custom molds can be quite high, making progressive die stamping less suitable for short-term production or prototype production.
Global Perspective
Progressive die stamping, with its numerous advantages, has been adopted worldwide. However, the extent of its adoption varies, with some regions emerging as leaders while others face challenges in embracing the technology. Let's explore the global landscape of progressive die stamping to understand these dynamics.
Leading Regions and Their Success Stories
Asia-Pacific Region (APAC):
Countries such as China, Japan, and South Korea have become powerhouses in manufacturing. Their rapid industrialization coupled with technological investments has made them leaders in the field of progressive die stamping.
Success Factors: The availability of skilled labor, robust infrastructure, government incentives for manufacturing, and a vast domestic market are all reasons why these countries have taken a dominant position.
North America:
The United States, with its rich industrial history and advanced technology, holds a significant place in the field of progressive die stamping.Success Factors: A high emphasis on research and development, funds available for investment, and a mature automotive industry have propelled its success in this field.
Europe:
Germany, Italy, and France have made significant contributions to the progressive die stamping sector, particularly in the automotive and aerospace industries.
Success Factors: A tradition of precision engineering, high-quality standards, and a focus on innovation have placed these countries at the forefront.
Global Adoption Barriers
Although progressive die stamping technology has been widely adopted, certain barriers hinder its global dissemination:
1. Infrastructure Limitations: Regions with underdeveloped industrial infrastructures may find it challenging to install and maintain the precision machinery required for progressive stamping.
2. Skill Gap: The successful implementation of this method requires skilled technicians and engineers. Areas lacking such specialized skilled personnel may face obstacles.
3. Economic Factors: The initial investment in progressive die stamping, especially in custom tooling, can be quite substantial. Regions experiencing economic difficulties may struggle to raise the necessary funds.
4. Regulatory and Compliance Issues: In some countries, strict regulations or bureaucratic practices may impede the adoption of new manufacturing methods.5. Cultural Barriers: In some regions, traditional manufacturing methods may be deeply ingrained, making the transition to new technologies such as progressive stamping challenging.
Impact on Small and Medium-sized Enterprises (SMEs) and the Supply Chain
The ripple effects of progressive die stamping extend beyond large manufacturers. Small and medium-sized enterprises (SMEs) and the broader supply chain can also feel its impact. Let's explore how this method can have both positive and negative effects on these industries.
Impact of Progressive Die Stamping on SMEs
Advantages
Cost-effectiveness: For SMEs capable of bearing the initial setup, progressive die stamping is an economically efficient method for producing parts, especially in bulk. The reduction in cost per part over time can save a significant amount of money.
Competitive advantage: By adopting progressive die stamping technology, SMEs can offer precision parts at competitive prices, allowing them to compete with larger rivals.
Scalability: Progressive die stamping provides flexibility for SMEs to quickly expand production scale in response to increased demand.Challenges
Initial Investment: For small and medium-sized enterprises (SMEs) with limited funds, the upfront costs of equipment and custom molds can be daunting.
Technical Expertise: SMEs may struggle to find or afford the skilled technicians required for progressive die stamping.
Market Dynamics: Particularly those SMEs serving niche markets may find that demand does not justify the investment in progressive die stamping.
Supply Chain Dynamics
Lead Time:
Reduction: The rapid production capabilities of progressive die stamping can significantly shorten delivery cycles, ensuring faster delivery of products to customers or downstream manufacturers.
Predictability: The consistency of this method makes delivery cycles more predictable, which aids in better planning and scheduling.
Inventory Management:Reduce Inventory: The production pace means that parts can be produced just in time, thereby reducing the need for large inventories.
Effective Use of Raw Materials: Progressive die stamping's efficient use of materials can reduce waste in inventory.
Overall Supply Chain Efficiency:
Simplify Operations: The high efficiency of this method from raw material suppliers to final product manufacturers can make the entire supply chain operation smoother.
Reduce Risks: The precision and consistency of progressive stamping can reduce the risk of defective parts, thereby reducing supply chain disruptions.
Save Costs: The cost-effectiveness of this method can save costs for the entire supply chain, benefiting both suppliers and customers.
Summary
Progressive die stamping has brought revolutionary changes to the manufacturing industry, integrating speed, precision, and cost-effectiveness. Although it has undeniable advantages, such as high-quality production and economic benefits, there are some challenges to consider, especially for small businesses facing initial investments. However, with technological advancements and the development of sustainability, the high efficiency and environmentally friendly characteristics of progressive die stamping make it a major choice for the future. In short, progressive die stamping represents the face of modern manufacturing and is expected to achieve growth and innovation in the coming years.
Comment