In the global manufacturing industry, achieving precision in large-scale metal stamping is both a challenge and a necessity. As demand surges, ensuring that each stamped component meets strict quality standards becomes crucial. However, how can manufacturers consistently maintain this level of precision?
To maintain precision in large-scale metal stamping, manufacturers employ advanced machinery, implement rigorous quality control measures, and provide ongoing training to their staff. By integrating these practices, they can ensure that the quality of each stamped component remains consistent, unaffected by production volumes.
Delve into the complexities of achieving precision in large-scale metal stamping and the strategies adopted by industry leaders.
The Role of Advanced Stamping Machines
In the field of metal stamping, the machines used play a pivotal role in determining the precision and quality of the final product. Over the years, the evolution of these machines has been revolutionary, ensuring that manufacturers can meet the increasing demands for precision, especially in mass production scenarios.
Evolution of Stamping Machines: From Manual Systems to CNC Systems
Advertisement
The development journey of stamping machines began with manual systems, where operators had to manually set up and operate the machines. While effective at the time, these systems had limitations in terms of speed, consistency, and accuracy. With technological advancements, the industry introduced Computer Numerical Control (CNC) systems. These machines, controlled by computer systems, brought about a paradigm shift in metal stamping. With CNC systems, manufacturers can achieve complex designs, tighter tolerances, and faster production speeds. Automation ensures that each stamped part is almost identical to the previous one, eliminating the inconsistencies commonly found in manual systems.How Modern Machinery Ensures Consistency in Force and Alignment
One of the standout features of modern stamping presses is their ability to apply consistent force throughout the entire stamping process. This is crucial because even minor variations in force can lead to defects or inconsistencies in the final product. Advanced sensors and feedback loops within these machines monitor the force in real-time and make fine adjustments as needed to maintain consistency.
Moreover, alignment is another critical factor in stamping. Modern machines are equipped with precision alignment systems that ensure the metal sheets are perfectly positioned before each stamping. This not only ensures the accuracy of each stamping but also reduces the likelihood of tool wear, thereby extending their service life.
The Significance of Regular Machine Maintenance and Calibration
Advanced machinery undoubtedly enhances the precision and efficiency of metal stamping, but it is essential to understand that these machines require regular maintenance and calibration to function optimally. Regular maintenance ensures that all components of the machine are in perfect working order, thereby reducing the occurrence of unexpected failures.
On the other hand, calibration is crucial for ensuring that the machine operates within the specified tolerances. Over time, even the most advanced machines can deviate from calibration due to regular wear. By regularly calibrating the machines, manufacturers can ensure that each stamp is as precise as the last, maintaining the high standards required by the industry.
Quality Control - The Pillar of Precision
In the realm of mass production of hardware stampings, achieving stable precision is not only about the machines or materials used but also about the monitoring systems in place to ensure quality at every step of the process. In this context, quality control becomes the pillar of precision, ensuring that each stamped component meets the expected specifications and standards.
Using Online Inspection Systems for Real-Time Quality Checks
One of the most effective ways to ensure precision in mass production of hardware stampings is by employing online inspection systems. These systems are typically equipped with advanced sensors and cameras that continuously monitor the stamping process in real-time. They can even detect the slightest deviations from the required specifications, allowing for immediate corrective actions. By identifying potential issues early, manufacturers can reduce waste and rework, ensuring that only high-quality components proceed to the next stage of production.The Role of Statistical Process Control (SPC) in Monitoring Production Quality
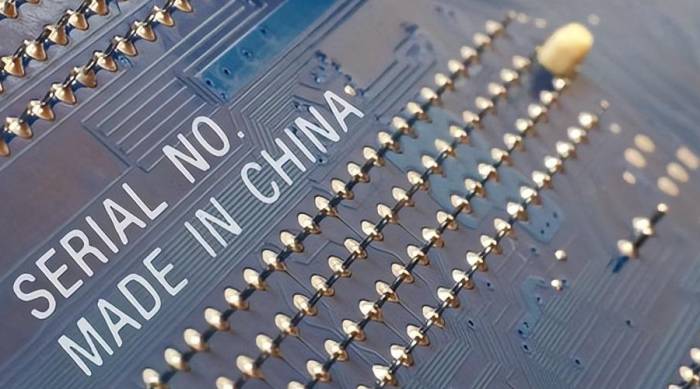
Statistical Process Control (SPC) is a method used for analyzing and controlling the quality of production processes. By collecting data from the production line and analyzing it using statistical methods, manufacturers can identify trends, variations, and potential issues. For instance, if a tool begins to wear out, it may cause the dimensions of stamped parts to change gradually. SPC can detect such trends early on, allowing for preventive maintenance or tool replacement before the problem escalates. This proactive approach ensures that production remains within the expected quality range and maintains precision at all times.
The Importance of Regular Audits and Third-Party Certifications
While internal quality control measures are essential, regular audits and third-party certifications provide additional assurance. External audits can conduct an impartial review of the production process, identifying areas for improvement that may be overlooked internally. Moreover, obtaining third-party certifications (such as ISO standards) indicates that the manufacturer adheres to globally recognized quality standards. These certifications not only enhance brand reputation but also instill confidence in customers and stakeholders regarding the quality and precision of the stamped parts.
Workforce Training and Skill Development
In the mass production of metal stamping, although machinery and technology play a crucial role, the human factor remains irreplaceable. Employees operate these machines with their skills and expertise, make decisions on the shop floor, and ensure that the final products meet the expected standards. Therefore, investing in their training and skill development becomes vital.
Continuous Training for Operating Advanced Machinery
As technology advances, the machines used for metal stamping are also continuously improving. To enhance precision and efficiency, new features, controls, and performance are regularly added. However, the effectiveness of these advanced technologies depends on the operators behind them. Continuous training ensures that employees are up-to-date with the latest machine functions. This enables them to maximize the potential of the equipment, ensure optimal performance, and minimize errors.Role-playing and Simulation Training for Real-world Scenarios
Simulation training is one of the most effective training methods. By recreating real scenarios in a controlled environment, workers can practice responding to various situations without the risk of causing actual production disruptions. On the other hand, role-playing helps to develop soft skills such as communication and teamwork. For instance, a role-playing scenario might involve a machine breakdown, where operators, maintenance teams, and floor managers must coordinate their actions. Such exercises not only improve technical skills but also foster collaboration and problem-solving abilities.
Encouraging a Culture of Quality and Precision Among Employees
In addition to technical training, instilling a culture of quality and precision among employees is also crucial. When everyone, from machine operators to quality inspectors, takes pride in the precision of their work, the overall quality of production naturally improves. Regular seminars, feedback sessions, and recognition programs can effectively promote this culture. Celebrating milestones, acknowledging individuals who consistently deliver high-quality work, and creating a platform for employees to share best practices can greatly ensure that the entire team aligns with the company's quality objectives.
The Impact of Material Selection on Precision
In the field of mass-produced metal stamping, the choice of material is not only about durability or cost-effectiveness. It is about precision. The material used can greatly affect the precision of the final product, especially in mass production, where even minor inconsistencies can lead to significant differences.
The Importance of Using Consistent High-quality Raw Materials
Each metal or alloy has its unique properties, ranging from ductility to tensile strength. Using high-quality raw materials ensures that these characteristics remain consistent throughout the production process. For example, impurities in metals can cause unexpected behavior during the stamping process, such as uneven bending or a higher propensity for cracks. By sourcing consistent, high-quality materials, manufacturers can ensure that the performance of each stamped part is predictable and maintains the required precision.
The Role of Material Testing in Ensuring Batch Consistency
Material testing plays a crucial role in ensuring consistency across batches. By conducting thorough tests on the raw materials, manufacturers can identify and mitigate potential issues before they affect the final product. This not only ensures that each batch meets the desired quality standards but also helps in maintaining a consistent level of precision across all products. Regular testing and quality control measures are essential to maintain the integrity of the materials and the final output.Even with the procurement of high-quality materials, variations can occur between different batches. This is where material testing becomes crucial. Before entering the production line, each batch of material can be tested for properties such as hardness, elasticity, and chemical composition. Such tests ensure that the materials meet the expected standards and can address any deviations before they affect the production process.
Addressing the Challenges of Different Metals and Alloys
Different metals and alloys present their own challenges. For instance, aluminum may be highly regarded for its light weight and ductility, but compared to steel, it is also more prone to deformation at high temperatures. On the other hand, metals with higher hardness, such as titanium, while possessing excellent strength, may require greater force during the stamping process, potentially affecting the lifespan of the dies.
To maintain precision, it is essential to understand these challenges and adjust the stamping process accordingly. This may involve adjusting machine settings, using specialized tools, or even altering designs to accommodate the material characteristics.
The Impact of Die Design on Precision
In the realm of high-volume metal stamping, the machines and materials used are undoubtedly critical. However, dies—the molds used to shape metal—play an equally significant role in ensuring precision. The design and maintenance of these dies greatly affect the accuracy and consistency of the stamped parts.
Designing Mold Parts for Reproducibility and Minimal Wear
Well-designed mold parts can consistently produce the same results batch after batch. This reproducibility is the cornerstone of precision in metal stamping. To achieve this, the design of mold parts must incorporate wear-resistant materials and geometries that can withstand immense pressure and friction during the stamping process. Additionally, the design of mold parts should facilitate the even distribution of force, ensuring that the metal is uniformly formed each time.
The Significance of Regular Inspection and Replacement of Dies
Even the best-designed dies will wear over time, especially in the context of high-volume production. As wear occurs, stamping precision can begin to deviate. Regular inspections can detect signs of wear before they affect product quality. By measuring tool dimensions, checking for signs of damage, and even using technologies such as laser scanning, manufacturers can determine when a die is nearing the end of its useful life. This allows for timely replacement or repair, ensuring uninterrupted precision.Innovations in Mold Materials and Design to Enhance Service Life
The world of metal stamping is not static. As challenges arise, so do innovations. There is ongoing exploration into the potential of new materials such as tungsten carbide (hardened steel) or advanced ceramics to extend the life of molds. These materials offer superior wear resistance compared to traditional tool steels, especially in demanding applications.
Furthermore, design methodologies are also advancing with the aid of computer simulations, enabling the creation of molds that optimize force distribution, reduce stress points, and enhance overall durability. These innovations not only extend the service life of molds but also ensure consistent precision throughout their lifespan.
Case Study: Success Stories in High-Volume Precision Stamping
Mastering the precision of high-volume metal stamping is a process filled with challenges, innovations, and continuous improvements. Some industries have set benchmarks in this area, demonstrating how to maintain precision during mass production of components. Let's delve into some successful cases across various industries.
How Automotive Giants Achieve Precision in Mass-Produced Components
The automotive industry's substantial demand for stamped parts is the best testament to high-volume precision stamping. Companies like Toyota and Volkswagen have implemented methods such as the Toyota Production System and lean manufacturing principles. These approaches emphasize waste reduction, continuous improvement, and meticulous quality control. For instance, Toyota's "andon" system allows any worker to stop the production line upon detecting a defect, ensuring that only precise parts enter the manufacturing process. This strict quality check, combined with state-of-the-art machinery, ensures consistent precision in the stamping of millions of automotive components.
Lessons from the Electronics Industry: Precision Stamping of Micro Components
The electronics industry, particularly in the fields of smartphones and microchips, requires the stamping of extremely small and complex parts. Companies like Apple and Samsung have mastered the technology to produce these tiny components with impeccable precision. Advanced micro-stamp techniques, combined with stringent quality control measures, ensure that every tiny connector, pin, or chip socket is stamped to exact specifications. The success of these companies in maintaining the precision of such micro components highlights the importance of innovation and quality control in high-volume stamping.Benchmark for Mass Precision Stamping in the Aerospace Industry
In the aerospace sector, even the slightest deviation can lead to severe consequences, hence the industry has set a high benchmark for precision stamping. Stamped components procured by companies like Boeing and Airbus must strictly adhere to international aerospace quality standards. These parts undergo rigorous testing, from tensile strength assessments to thermal simulations, to ensure they meet the stringent criteria of the aerospace industry. The ability of these aerospace giants to maintain precision even in mass production highlights the importance of strict quality standards and rigorous testing protocols.
Harnessing Advanced Technology to Enhance Precision
In the ever-evolving manufacturing industry, staying ahead is crucial, especially when precision is of utmost importance. The integration of cutting-edge technology has revolutionized the way mass metal stamping is done, ensuring higher precision and efficiency. Let's explore some of these technological advancements and their impact on precision.
The Role of Artificial Intelligence and Machine Learning in Predictive Maintenance
Artificial Intelligence (AI) and Machine Learning (ML) have made significant strides in the manufacturing industry, particularly in predictive maintenance. By analyzing vast amounts of data from stamping machines, AI algorithms can predict when a machine might fail or when a tool might wear out. This proactive approach ensures maintenance is scheduled before a breakdown occurs, minimizing downtime and ensuring consistent precision. Additionally, ML models learn from past defects and inefficiencies, continually improving the stamping process over time.
The Prospects of Robotics in Mass Metal Stamping
Robots, capable of working tirelessly and maintaining consistent precision, are becoming indispensable tools in the metal stamping industry. Advanced robotic arms equipped with sensors can handle complex stamping tasks with an accuracy that is beyond human capability. As these robots become more sophisticated, they can adapt to changes in the stamping process in real-time, ensuring precision is maintained even in mass production. Moreover, collaborative robots (or "cobots") are designed to work alongside humans, combining the strengths of both to achieve unparalleled precision.
How Digital Twins and Simulations Aid in Achieving Precision
The concept of "digital twins"—virtual replicas of physical products, processes, or systems—has been widely adopted in the manufacturing sector. In terms of metal stamping, digital twins can simulate the entire stamping process, allowing manufacturers to identify potential issues before they arise in the real world. By adjusting the simulation, they can optimize the stamping process to achieve the highest precision. Additionally, real-time simulations can provide feedback during the stamping process for immediate adjustments, maintaining precision.Conclusion
Maintaining the precision in large-scale metal stamping is a multifaceted challenge that requires the perfect combination of advanced technology, skilled labor, and stringent quality control measures. As the industry evolves, adopting these best practices will be key to achieving unparalleled precision, regardless of production volume.
Comment