Delve into the intricate world of progressive die stamping, a marvel of modern manufacturing. How does this technology meet the manufacturing requirements for complex parts, and what makes it unique in the field of metal stamping?
Progressive die stamping is an advanced method that processes metal sheets sequentially through a series of stations, each performing a specific action, to produce complex parts. It is renowned for its efficiency, precision, and the ability to easily handle complex designs.
But what is the mystery behind this method? How does it perfectly present complex designs? Let's uncover the mechanical principles, advantages, and nuances of progressive die stamping.
**Progressive Die Stamping (Progressive Stamping)**
In the vast field of metalworking and manufacturing, progressive die stamping stands as a beacon of modern innovation. Although the operation is complex, it offers unparalleled efficiency and precision, especially when producing complex parts. With the development of various industries and the demand for complex components, the importance of progressive stamping in today's manufacturing cannot be overstated.
Advertisement
**Unveiling the Process**
As the name suggests, progressive die stamping is a continuous process. It involves feeding a metal strip into a series of stations, each performing a specific operation, until the final part is produced. Here is a step-by-step breakdown:
Feeding: The metal strip is fed into the stamping press.
**Step 1: Feeding**
The process begins with the feeding of the metal strip into the stamping press. This is the first station where the raw material is introduced into the system.
**Step 2: Piercing**
In the next station, the metal is pierced to create holes or cutouts as per the design requirements. This is done using a punch and die set that are precisely aligned to ensure accuracy.
**Step 3: Forming**
Following the piercing, the metal is formed into the desired shape. This can involve bending, drawing, or other forming processes that are specific to the part's design.
**Step 4: Trimming**
Once the part has been formed, any excess material is trimmed away. This ensures that the part meets the exact specifications and is ready for the next stage of production.
**Step 5: Final Operations**
The final stations may include operations such as bending, flanging, or any other finishing processes required to complete the part.
**Step 6: Ejection**
The completed part is then ejected from the die, ready for further processing or assembly.
**Advantages of Progressive Die Stamping**
1. **High Efficiency**: The process is highly automated, allowing for quick production of parts with minimal manual intervention.
2. **Precision**: The use of precision tools and machines ensures that each part is produced to exact specifications.
3. **Cost-Effective**: The ability to produce parts in large quantities with minimal waste makes progressive die stamping a cost-effective solution.
4. **Complex Design Capability**: The technology can handle intricate designs that would be difficult or impossible to achieve with traditional stamping methods.
**Subtleties of Progressive Die Stamping**
1. **Tooling Complexity**: The tooling for progressive dies is more complex and requires skilled design and engineering.
2. **Setup Time**: While the production is fast, the initial setup for a progressive die can be time-consuming and costly.
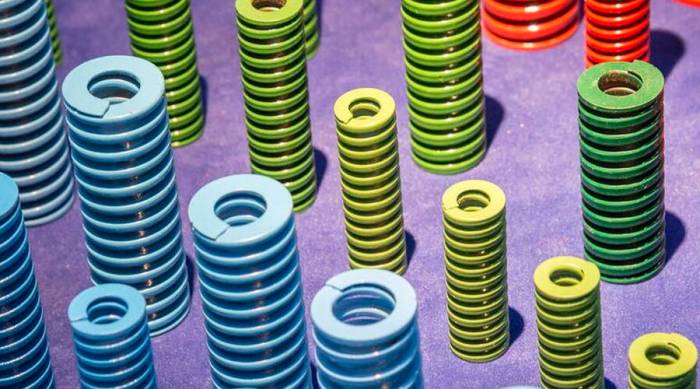
3. **Material Thickness**: Progressive dies are typically designed for a specific material thickness, which can limit flexibility in production.
Understanding the intricacies of progressive die stamping is crucial for anyone involved in the manufacturing of complex metal parts. Its combination of efficiency, precision, and design flexibility makes it an invaluable tool in the modern manufacturing landscape.Localization: The metal strip is correctly positioned using a guide pin.
Stamping: As the metal strip advances, it passes through a series of stations. Each station performs a specific operation, such as stamping, bending, forming, or cutting.
Continuous: After each action, the strip moves on to the next station, each step bringing it closer to its final shape.
Ejection: Once the part has passed through all stations and is fully formed, it is separated from the strip and ejected.
The heart of this process is the die—a tool specifically designed for stamping. The "progressive" nature of the stamping die refers to its multiple stations, each with a specific task, ensuring that the metal undergoes a series of transformations in a single stamping.
Why complex parts?
The charm of progressive die stamping lies in its ability to produce precision complex parts. But what makes it particularly suitable for intricate designs?
Repeatability: This method is designed for mass production. Once set up, it can produce tens of thousands or even millions of identical parts, each one perfectly aligned with the design specifications.
Efficiency: Continuous feeding and multi-station design mean that multiple parts can be processed simultaneously. Thus, the production speed is very fast, making it ideal for large-volume orders.Save materials: This process is designed to minimize waste. Its progressive nature ensures that as much of the metal strip as possible is used in the final product.
Compared to other stamping methods, continuous stamping stands out for its ability to handle complex designs in an economical and efficient manner. While methods such as transfer die stamping or single stamping also have their advantages, they typically require more manual intervention or are more suitable for large parts. For intricate, complex parts, especially those produced in large quantities, continuous stamping is the preferred choice for many manufacturers.
Advantages of continuous die stamping for complex parts
Continuous stamping offers a multitude of advantages with its complex and efficient process, especially when it comes to processing complex parts. These advantages not only ensure top-notch product quality but also contribute to sustainable and cost-effective production. Let's delve deeper into these main advantages:
Precision and consistency
One of the standout features of continuous stamping is its unparalleled precision. Here's how it ensures that each part is a mirror image of the others:
Tailor-made dies: Each die is carefully designed to meet the exact specifications of the part. This ensures that every stamping, bending, or punching is precise down to the smallest detail.
Automated processes: The automation process eliminates the inconsistencies that can arise from manual operations. This means that whether it's the first part or the ten thousandth part, each one will be identical to the last.
Quality control: Modern stamping machines are typically equipped with sensors and monitoring systems that continuously check for any deviations in the parts, ensuring that any anomalies are detected and corrected immediately.Speed and Efficiency
In the fast-paced manufacturing industry, time is of the essence. Continuous stamping shines in this regard:
Simultaneous Operations: As the metal strip passes through the dies, multiple operations are carried out at different workstations simultaneously. This parallel processing significantly reduces the time required to produce each part.
Continuous Feeding: The continuous feeding of the metal strip ensures no downtime between part production, achieving a seamless and rapid production cycle.
Cost-Effective: The speed and efficiency of the process can reduce production costs, especially when producing parts in large quantities. The initial setup may consume a significant amount of resources, but the long-term benefits are substantial in terms of reducing the cost per unit.
Waste Reduction
In an era where sustainable development is crucial, the ability of continuous stamping technology to reduce waste is undoubtedly a great boon:
Optimized Material Usage: The design of the dies and the process ensures maximum utilization of the metal strip in the final product, minimizing offcuts and waste.
Recycling: Any waste generated, such as offcuts or parts punched out, can be easily collected and recycled, ensuring minimal material waste.
Environmental Benefits: Reducing waste means fewer resources are needed to produce the same number of parts. Coupled with recycling, this ensures that the impact of the manufacturing process on the environment is minimized to the greatest extent possible.The Challenges and Considerations of Progressive Die Stamping
While progressive die stamping offers numerous advantages, it is not without challenges. Like any manufacturing process, it requires careful consideration and understanding of its limitations to fully harness its potential. Let's delve into some of the challenges and considerations associated with this method:
Design Limitations
Every manufacturing technique has its limitations, and progressive die stamping is no exception:
Complexity Constraints: Although this method is ideal for complex parts, the level of complexity it can handle is limited. Extremely intricate designs may require multiple dies or other methods.
Material Thickness: Progressive die stamping is best suited for materials of specific thicknesses. Materials that are too thick or too thin can present challenges for die design and stamping efficiency.
Die Design: The design of the die itself is also challenging. It needs to take into account the properties of the material, the required final shape, and the sequence of operations.
Tips for Optimizing Design
... (The rest of the text is not provided, so the translation cannot be completed.)Collaboration: Work with experienced die designers during the product design phase to ensure the feasibility of progressive stamping design.
Prototype Design: Create prototypes to test the design and make necessary adjustments before finalizing the die.
Material Considerations: Consider factors such as ductility and tensile strength to select materials suitable for the stamping process.
Maintenance and Wear
The continuity and high speed of progressive die stamping mean that the dies will experience significant wear:
Regular Wear: Each stamping action, though minor, causes wear on the die. Over time, this can lead to a decrease in the precision and quality of the stamped parts.
Lubrication: Friction between the die and the metal strip accelerates wear. Regular lubrication is crucial for reducing friction and extending the die life.
Material Issues: Using materials harder than the die or contaminants in the material can lead to premature wear or even damage.Maintenance Tips
Regular Inspections: Regularly check the mold for signs of wear or damage. Early detection can prevent more serious issues from arising.
Routine Maintenance: Establish a daily maintenance plan. This includes cleaning, lubricating, and minor repairs.
Spare Parts: Keep necessary replacement parts on hand. This ensures minimal downtime in case of wear or damage.
The Future of Progressive Die Stamping
Driven by technological advancements and innovative practices, the manufacturing industry is constantly evolving. Progressive die stamping, a backbone in the metalworking sector, is no exception. Looking ahead, several emerging trends and technologies are poised to redefine the face of this ancient technique.
Technological Advancements
Artificial Intelligence (AI): AI is expected to play a transformative role in the field of progressive die stamping. By analyzing vast amounts of data, AI can predict wear, adjust parameters in real-time for optimal results, and even assist in the design of molds for maximum efficiency and precision, thereby optimizing the stamping process.
Advanced Sensors and Monitoring: The integration of advanced sensors can provide real-time feedback during the stamping process. This can lead to immediate adjustments, ensuring consistent quality and reducing waste. For instance, sensors can detect material inconsistencies or temperature fluctuations that may affect the quality of the stamping.Robotics and Automation: Although continuous die stamping is already an automated process, integrating advanced robotic technology can further enhance precision, especially for complex parts. Robots can handle materials more accurately, ensure optimal positioning, and even assist with maintenance tasks.
Three-Dimensional (3D) Printing: Traditionally used for prototyping, advancements in 3D printing materials and technology may enable its combination with stamping. For instance, creating specific parts of molds or even producing small batches of stamped components.
Forecast for the Next Decade
Virtual Reality (VR) and Augmented Reality (AR) Technology: These technologies have the potential to revolutionize the design phase, allowing engineers to visualize and test mold designs in a virtual environment before production.
Focus on Sustainability: As the global industry shifts towards sustainable development, we can anticipate innovations in continuous die stamping technology to reduce energy consumption, minimize waste, and use environmentally friendly materials.
Customization: With technological advancements, the production of small-batch customized stampings may become more cost-effective, thus meeting the needs of niche markets and specific customer requirements.
Collaborative Manufacturing: More collaborative manufacturing approaches may emerge in the future, with continuous stamping seamlessly integrated with other technologies and processes to achieve an integrated production method.
Conclusion
In summary, while we have explored the profound impact of continuous die stamping technology on the manufacturing of complex parts, it is clear that its development journey is far from over. As we stand on the cusp of a new era in manufacturing, continuous die stamping technology not only holds its ground but also beckons a future filled with innovation, progress, and endless possibilities. This demonstrates the timeless significance of this ancient technique and its boundless potential for the future.
Comment