Explore the transformative role of automation in the metal stamping industry. How has this technological marvel reshaped traditional practices, improved efficiency, and set new industry benchmarks?
Automation has firmly taken root in the modern metal stamping field, driving unparalleled precision and consistency. Through integration, production speeds have significantly increased to meet market demands with new efficiencies. Additionally, the substantial reduction in human errors highlights the key role of automation in enhancing product quality standards.
Peeling back the layers of automation's clear advantages in the metal stamping sector, you will discover a world rich in detail and broad in impact. How does automation adjust the stamping process? What are its wider impacts on manufacturing? As we step into a new industrial chapter, how will the role of automation in metal stamping evolve? Join us in delving into the nuances and envisioning the future of manufacturing.
Introduction to Metal Stamping and Automation
The essence of metal stamping lies in the manufacturing process of shaping flat metal sheets into various forms using dies. This ancient technique has long been the backbone of numerous industries, from automotive to electronics, providing crucial components that bring their products to life. While traditional stamping methods are effective, they are often labor-intensive with limited precision and repeatability.
Advertisement
Automation—this technological marvel began reshaping the manufacturing landscape. As industries across the board pursued higher efficiency, consistency, and scale, automation emerged. In the metal stamping field, automation introduced robotic arms, computer-controlled processes, and advanced machinery, each aimed at increasing precision and speed. This evolution is not just about replacing human labor but about enhancing the entire process to meet the demands of modern manufacturing. As we trace the development of automation in metal stamping, we witness a story of innovation, adaptation, and relentless pursuit of excellence.
Historical BackgroundTracing back through history, metal stamping is a craft honed by skilled artisans, primarily relying on manual labor and rudimentary tools. Each stamped piece is a testament to the craftsman's expertise, with techniques passed down through generations. The workshop resonates with the rhythmic sound of metal striking, each impact transforming raw sheet metal into functional components.
However, with the expansion of industry and the surge in demand, the limitations of these traditional methods became quite apparent. Manual stamping is not only time-consuming but also prone to inconsistencies. The precision of each part largely depends on the artisan's skill, leading to varying quality. Production capacity is limited by human endurance, and scaling up often means a significant increase in labor and resources.
Moreover, traditional methods also pose safety risks. Due to the repetitive nature of the work and proximity to heavy machinery, workers are at risk of injury. The lack of standardization also means that quality assurance has always been a challenge.
Essentially, while traditional metal stamping processes have their charm and craftsmanship, it is undeniable that a more efficient, consistent, and scalable solution is needed. This has paved the way for the rise of automation, which is expected to meet challenges and propel the industry into a new era of excellence in manufacturing.
**Main Advantages of Metal Stamping Automation**
Incorporating automation into the metal stamping process has brought numerous benefits, changing not only the production process but also the nature of production itself. Let's delve deeper into the main advantages brought by automation:
1. Enhanced Precision and Consistency: With computer-controlled machines and advanced sensors, each die can execute with pinpoint accuracy. The days of variations and discrepancies are gone. Automation ensures that every metal part produced is identical to the last, achieving a level of consistency that manual methods cannot guarantee.
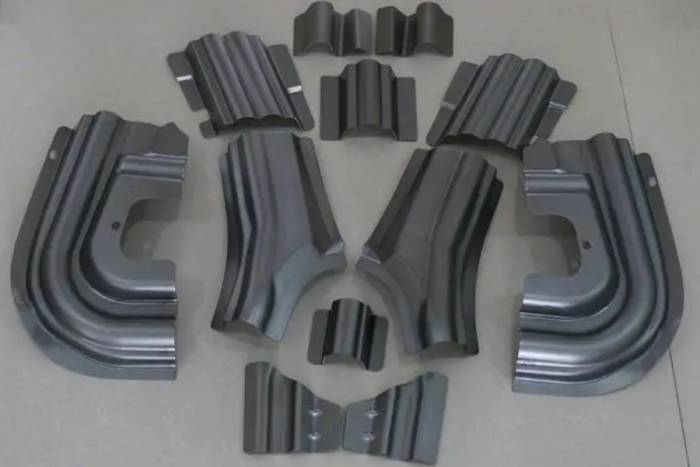
2. Increased Production Speed and Output: The operating speed of automatic stamping machines is extremely fast, with a production rate of parts that is unimaginable with manual setups. The increase in production capacity means that various industries can fulfill larger orders in a shorter amount of time, meeting the growing demands of the market.3. Reduce labor costs and human errors: Automation significantly reduces the reliance on manual labor, thereby saving a substantial amount of labor costs. Moreover, with the assistance of machinery, the likelihood of human errors is greatly diminished—such as misplacement, incorrect measurements, and so on. This not only ensures higher quality but also reduces waste.
4. Improve safety measures: One of the most commendable advantages of automation is the enhanced safety it brings to the workshop. Robotic arms and automated machinery are equipped with safety features that prevent accidents. Workers are no longer in close proximity to heavy machinery, thus reducing the risk of injury. Additionally, the elimination of repetitive strain associated with manual stamping ensures a healthier work environment.
In summary, the automation of metal stamping is not just a modernization of the process, but an optimization of it. It aims to achieve a synergistic enhancement of speed, precision, and safety, setting new benchmarks for the development of the global manufacturing industry.
---
Case Study: Modern Metal Stamping Equipment
Background
PrecisionTech Stamping, "located in the industrial heartland of Ohio, was once a traditional metal stamping factory. The company, established in the 1970s, primarily relied on manual operations, with employees proficient in the ancient stamping techniques. However, by the beginning of this century, the factory faced increasing challenges—rising demand, increasing labor costs, and intensifying competition from technologically advanced rivals.
Transition to Automation
In 2010, the management of PrecisionTech decided to invest in automation. They introduced computer numerical control (CNC) machines, robotic arms for material handling, and advanced sensors for quality control. The transformation was not only in the machinery but also in the workforce; employees were trained to operate and maintain the new automated systems.
Results1. Enhance Production Capacity: After automation, PrecisionTech's productivity has increased by 70%. They can now handle larger orders and deliver within shorter lead times.
2. Consistent Quality: Post-automation, every stamped component meets the company's stringent quality standards. The defect rate has dropped below 0.5%.
3. Cost Savings: Despite significant initial investments, the company's operational costs have been reduced. Labor costs have been lowered by 40%, and savings have also been achieved through waste reduction and efficient energy consumption.
4. Safety and Morale: The number of work-related accidents has decreased significantly. Additionally, employees who have acquired new skills now have higher morale and job satisfaction.
5. Market Position: Automation has elevated PrecisionTech's market position. They have secured contracts in high-precision industries such as aerospace and medical equipment.
The transformation of PrecisionTech's stamping company demonstrates the power of automation. This is a real-life example that underscores the tangible benefits automation brings to metal stamping equipment—defining operations, enhancing outcomes, and ensuring competitive advantage in a dynamic market environment.
Challenges and Considerations:
While the advantages of integrating automation into metal stamping are undeniable, there are also a series of challenges and considerations during the transition process. It is essential to view this transformation from a holistic perspective, understand potential obstacles, and develop corresponding plans. Let's delve into some of the main challenges and considerations of metal stamping automation:
1. Initial Investment and Cost ImpactChallenge: The primary challenge many factories face is the substantial initial investment required for the procurement and installation of automated systems. Advanced mechanical equipment, robotic arms, and computer control systems come at a high price.
Consideration: Although the upfront costs are significant, it is crucial to view them as a long-term investment. Over time, the efficiency and cost savings brought by automation can offset the initial expenditure.
2. Training and Skill Enhancement for Employees
Challenge: Automation introduces new technologies and processes that the existing workforce may not be familiar with. There is an urgent need for training and skill enhancement to ensure smooth operations.
Consideration: Investing in comprehensive training programs is essential. This not only equips employees with the necessary skills but also boosts morale, ensuring that employees feel valued and are seen as an indispensable part of the company's future.
3. Maintenance and Updates
Challenge: While automated machinery is robust and durable, it requires regular maintenance to ensure optimal performance. Additionally, as technology evolves, systems may need to be updated or even replaced to stay current.
Consideration: Establishing a dedicated maintenance team and scheduling regular checks can reduce potential failures. Budgeting for future updates and keeping abreast of technological advancements can ensure that facilities remain at the forefront of innovation.
4. Adapting to New Operational Dynamics
Challenge: Automation changes the operational dynamics of a facility. Workflow patterns may shift, and roles and responsibilities may undergo transformation.
Consideration: It is important to plan for these changes by reevaluating job roles and responsibilities. This may involve retraining employees for new tasks or reorganizing teams to align with the new operational structure. Ensuring that the workforce is adaptable and prepared for these changes is key to a successful transition to an automated environment.Considerations: Effective communication is key. Keeping employees informed about changes, soliciting their feedback, and ensuring a smooth transition can help adapt to new operational models.
While the path to automation is fraught with challenges, it is not insurmountable. With careful planning, foresight, and a commitment to continuous improvement, metal stamping equipment can meet these challenges and fully leverage the potential of automation.
**The Balance Between Humans and Machines**
In the age of automation, there is a common belief that machines will eventually replace the role of humans, rendering many jobs obsolete. However, the reality, especially in specialized fields such as metal stamping, is much more nuanced. The relationship between humans and machines is symbiotic, with each complementing the other's strengths. Let's delve into the ongoing importance of human expertise in an increasingly automated environment:
1. **Inherent Human Qualities**
Machines excel at precision, consistency, and speed. Yet, they lack the inherent intuition, creativity, and problem-solving abilities that humans possess. For instance, while machines can execute tasks flawlessly, it is human operators who can detect anomalies, make judgments, or propose innovative solutions to unforeseen challenges.
2. **Machine Supervision and Decision-Making**
No matter how advanced, automated systems require human supervision. It is human operators who calibrate, program, and monitor these machines to ensure they operate at peak performance. Human intervention is crucial for making wise decisions when machines encounter unfamiliar situations.
3. **Emotional Intelligence and Customer Relations**
Emotional intelligence plays a vital role in customer relations, an area where machines cannot compete with humans. Human operators can empathize with customers, understand their needs, and build relationships that foster loyalty and trust. This human touch is invaluable in maintaining customer satisfaction and business success.
In conclusion, while automation brings efficiency and scalability, the human element remains indispensable for innovation, problem-solving, and maintaining strong customer relationships. The future of metal stamping and other industries lies in the harmonious integration of human expertise and technological advancements.Although machines can handle production tasks, in fields that require emotional intelligence, human expertise is irreplaceable. Establishing customer relationships, understanding the specific needs of customers, and providing personalized solutions, in these areas, the human touch remains the most important.
4. Continuous Learning and Adaptation
The world of automation is constantly evolving. As new technologies emerge, the human workforce needs to learn, adapt, and integrate these advanced technologies into existing setups. Their ability to grow alongside technology ensures that equipment is always at the cutting edge.
5. Ethical Considerations
Automation brings a range of ethical considerations, from job displacement to safety standards. The human element in businesses must strive to address these issues, ensuring that the transition to automation is both gradual and humane.
Although automation has transformed the face of metal stamping, the role of human technical expertise remains as important as ever. This is not a battle between man and machine, but a harmonious collaboration between man and machine, each amplifying the other's capabilities to achieve unparalleled excellence.
The Future of Metal Stamping Automation
As we stand on the precipice of a new era in manufacturing, the potential of emerging technologies to reshape the metal stamping industry is both exciting and profound. Automation integration has already brought significant progress, but the process is far from over. Let's explore the future trajectory of metal stamping automation and the innovations that are on the horizon:1. Emerging Technologies and Their Potential Impacts
3D Printing: Traditionally associated with plastics, advancements in metal 3D printing technology could revolutionize the prototyping and low-volume production of metal stamping. This technology enables rapid design changes and customization, shortening the time from concept to product.
Internet of Things (IoT): Interconnecting machines through the Internet of Things can make factories smarter. Sensors can monitor the health of machines in real-time, predict maintenance needs, optimize production processes, and ensure the longest uptime and highest efficiency.
Augmented Reality (AR): AR can help operators intuitively understand complex processes, conduct training, and troubleshoot. By overlaying digital information on the physical world, AR can improve accuracy and reduce errors.
2. The Role of Artificial Intelligence Robots
Predictive Analytics: AI robots can analyze vast amounts of production data to predict defects, optimize processes, and improve quality. By identifying patterns and anomalies, these systems can proactively address issues before they escalate.
Adaptive Production: AI can dynamically adjust production parameters based on real-time feedback. For example, if sensors detect a change in material thickness, the system can immediately adjust the stamping pressure.
Enhanced Quality Control: AI-driven vision inspection systems can detect minute defects that the human eye might miss, ensuring that every product meets the highest quality standards.
Supply Chain Optimization: AI can predict demand, manage inventory, and optimize the supply chain, ensuring that resources are used effectively and production schedules are achieved.
3. Sustainable Development and Green Manufacturing
Sustainable development and green manufacturing are becoming increasingly important in the industry. Companies are focusing on reducing waste, conserving energy, and minimizing environmental impact. This includes the use of eco-friendly materials, implementing energy-efficient processes, and ensuring that products are designed with end-of-life considerations in mind. By adopting sustainable practices, manufacturers can reduce their carbon footprint, comply with environmental regulations, and appeal to consumers who value eco-conscious products.As industries worldwide strive to address environmental concerns, the future of metal stamping will also shift towards sustainable development. Automation plays a key role in reducing waste, optimizing energy consumption, and promoting recycling.
Conclusion
In summary, as we celebrate the milestone achievements of hardware stamping automation, we also eagerly anticipate the future—where technology and human ingenuity will together create unparalleled excellence. The story of hardware stamping is far from over; in fact, the most exciting chapters are yet to come.
Comment