Introduction: The Imperative of Sustainable Manufacturing
In the rapidly evolving industrial landscape of today, the pursuit of sustainable manufacturing has become not just an ideal goal but an urgent necessity. With the increasing severity of environmental issues and the depletion of resources, the demand for manufacturing practices that are ecologically balanced and resource-efficient has never been stronger. This study delves into a comparative analysis of two renowned machining technologies—Wire Electrical Discharge Machining (WEDM) and milling—to explore their respective contributions to sustainable manufacturing and to provide valuable insights into their environmental, economic, and social impacts.
Wire Electrical Discharge Machining (WEDM): Pulse Precision
Wire Electrical Discharge Machining (WEDM) is a revolutionary machining process that uses controlled electrical discharges to erode material from the workpiece. It is renowned for its exceptional precision, the ability to create complex geometric shapes, and minimal heat-affected zones. When we examine wire cutting from a sustainability perspective, several noteworthy aspects emerge:
Material Efficiency
Wire cutting operates in a non-contact manner, thereby minimizing material waste during the machining process. Compared to traditional techniques, this inherent feature enhances its material efficiency. Furthermore, wire cutting can machine hard and brittle materials, often leading to further material savings due to reduced scrap and rework.
Advertisement
Energy Consumption
Although the discharges in wire cutting consume a significant amount of energy, the material removal efficiency helps offset this energy consumption, potentially making it energy-neutral. Advances in power supply technology and pulse strategies also contribute to reducing the energy requirements of wire cutting.
Environmental Impact
While the discharges in wire cutting can generate waste materials, the process is generally cleaner compared to traditional machining methods, which often involve the use of coolants and lubricants that can be harmful to the environment. The lack of such substances in wire cutting reduces the environmental footprint and contributes to a cleaner manufacturing process.
Milling: Material Removal and Precision
Milling is a versatile machining process that involves the removal of material by feeding a workpiece into a rotating cutting tool. It is widely used for its precision and ability to produce complex shapes with a high degree of accuracy. When considering milling in the context of sustainable manufacturing, the following aspects are significant:
Material Efficiency
Milling can achieve high material removal rates, which can lead to efficient use of resources. However, the process can generate a significant amount of waste, especially when machining complex shapes. The use of high-speed milling and advanced tooling can help minimize waste and improve material efficiency.
Energy Consumption
Milling typically consumes less energy than wire cutting due to the nature of the process, which involves mechanical rather than electrical energy. However, the energy efficiency can vary depending on the type of milling operation, the machine used, and the materials being processed.
Environmental Impact
Milling can have a substantial environmental impact due to the use of coolants and lubricants, which can contribute to pollution if not managed properly. The adoption of dry or near-dry milling techniques can help reduce the environmental footprint of the process.
In conclusion, both WEDM and milling have their advantages and challenges when it comes to sustainable manufacturing. WEDM excels in precision and material efficiency but requires careful management of energy consumption and waste materials. Milling offers versatility and high material removal rates but must address the issues of waste generation and the use of coolants. By understanding these aspects, manufacturers can make informed decisions to optimize their processes for sustainability.In the process of electrical discharge wire cutting, the use of dielectric fluids needs to consider environmental factors. However, managing the use of dielectric fluids responsibly and exploring environmentally friendly alternatives can mitigate this impact. Moreover, the precision of wire cutting reduces the need for post-processing operations, such as grinding, which would consume additional energy and resources.
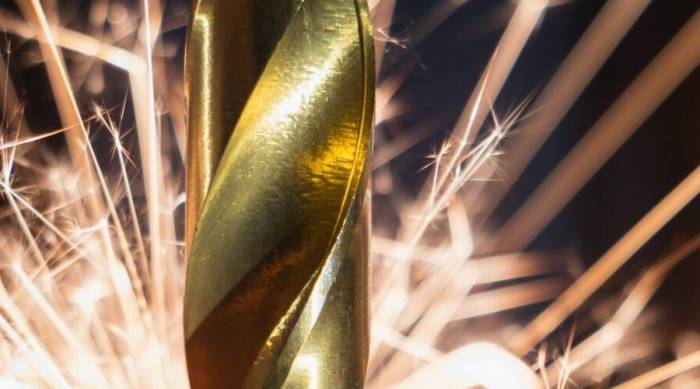
Milling: Carving through Subtraction
Milling is a widely used subtractive manufacturing process that shapes and carves materials using a rotating cutting tool. Its versatility in material removal, tool selection, and adaptability makes it a mainstay in various industries. When assessing the sustainability of milling, the following factors come into play:
Material Efficiency
Compared to wire cutting, milling, due to its subtractive nature, may lead to more severe material waste. Prudent material management practices are crucial for improving its sustainability in this regard. CNC machining, high-speed machining, and optimized tool paths are strategies that can be employed to reduce material waste.
Energy Consumption
The kinetic energy required for rotation and cutting makes milling a moderately energy-intensive process, but advancements in machine efficiency help reduce energy consumption. Regenerative braking systems, more efficient spindle designs, and the use of renewable energy sources are ways to minimize energy consumption.
Environmental Impact
Strategically selecting cutting parameters and tools, coupled with optimized machining techniques, can significantly reduce waste generation and energy consumption during the milling operation. Additionally, the integration of a coolant management system can lessen the environmental impact associated with the use of coolants.Comparative Sustainability Analysis: A Three-Dimensional Discourse
Environmental Impact
Both wire cutting and milling processes have distinct environmental footprints. The dielectric fluid used in wire cutting and the material waste from milling contribute to their respective impacts. Implementing dielectric fluid recovery and adopting precision machining strategies for milling can mitigate these effects. Furthermore, advancements in additive manufacturing and hybrid machining processes have the potential to redefine the environmental sustainability of manufacturing.
Economic Considerations
The economic aspect of sustainability is crucial for manufacturing processes. The extended tool life and precision offered by wire cutting machines provide cost-effectiveness, while the lower setup costs and operational flexibility of milling offer economic advantages. A comprehensive cost-benefit analysis is essential for process selection. Additionally, the circular economy concept, which emphasizes reuse and recycling, can enhance the economic viability of both technologies.
Social Aspects
The human factor in manufacturing cannot be overlooked. The automation potential of wire cutting processes may impact employment opportunities, while the reliance on skilled operators in milling contributes to workforce development. Striking a balance between technological advancement and social welfare is crucial for sustainable manufacturing. Enhancing workers' skills in operating and maintaining advanced machinery and fostering a culture of innovation can bridge the gap between technological progress and job preservation.
Charting a Trajectory for Sustainable DevelopmentIn the pursuit of sustainable manufacturing, a comprehensive approach that encompasses environmental, economic, and social aspects must be adopted. This study provides a thorough comparative assessment of wire cutting and milling, revealing their contributions to sustainable development. Each technology has its strengths and weaknesses, yet both hold the potential to drive a sustainable transformation. Industries can fine-tune their processes for optimal sustainability through techniques such as Design of Experiments (DOE) and Life Cycle Assessment (LCA). As technology continues to advance, precision, efficiency, and sustainability will shape a manufacturing landscape that thrives on innovation while protecting the Earth's fragile ecosystems.
Future Outlook: Shaping Sustainable Manufacturing
As we look to the future of manufacturing, it is clear that sustainable practices will play an increasingly critical role. The integration of Industry 4.0 technologies such as the Internet of Things (IoT), Artificial Intelligence (AI), and data analytics is expected to usher in a new era of manufacturing. By enabling real-time monitoring, predictive maintenance, and process optimization, these technologies can significantly improve resource utilization, minimize downtime, and reduce waste. The convergence of the digital and physical realms, often referred to as the "smart factory," can lead to more streamlined and environmentally friendly production systems.
Moreover, the development and implementation of green materials will bring about a paradigm shift in manufacturing. These materials, typically sourced from renewable resources or easily recyclable, can significantly reduce the environmental impact of wire cutting and milling processes. Advances in material science and nanotechnology open the door for materials that enhance mechanical performance and reduce energy demands, further promoting sustainable manufacturing practices.
Policy and Collaboration: Paving the Way for Sustainable Development
The journey towards sustainable manufacturing cannot be embarked upon by industry alone. Collaboration between academia, industry stakeholders, and policymakers is crucial for creating a conducive environment for sustainable practices. Governments around the world are increasingly recognizing the importance of sustainable development and are implementing policies that incentivize eco-friendly manufacturing. Tax incentives, R&D grants, and stricter environmental regulations are some policy tools that can shape sustainable manufacturing practices.
Furthermore, collaboration between academia and industry can drive research and innovation in sustainable manufacturing. Joint research projects can explore new materials, process optimization techniques, and recycling methods, fostering a culture of continuous improvement. The sharing of knowledge, best practices, and technological breakthroughs will facilitate the transition to a more sustainable manufacturing landscape.Balancing Innovation and Tradition: A Holistic Approach
While the allure of cutting-edge technology and futuristic concepts is undeniable, striking a balance between innovation and traditional wisdom is crucial. Embracing the principles of a circular economy, which involves protecting resources through reuse, refurbishment, and recycling, can serve as a beacon for sustainable manufacturing. Both wire electrical discharge machining (WEDM) and milling can benefit by adopting circular economy principles to extend tool life, refurbish components, and promote material recycling and reuse.
In the grand blueprint of sustainable manufacturing, every stakeholder has a role to play. From engineers and designers creating efficient processes to consumers choosing sustainable products, collective efforts towards sustainable development resonate throughout the entire supply chain. As consumer awareness of sustainability grows, the market for eco-friendly products continues to expand. Manufacturers who prioritize sustainability not only contribute to a healthier planet but also position themselves as leaders in the market of consciousness and ethics.
Conclusion: Crafting a Greener Tomorrow
In the grand symphony of industrialization, the melody of sustainability takes center stage. A comparative study of wire electrical discharge machining (WEDM) and milling elucidates the path towards more sustainable manufacturing practices. While each method possesses unique attributes and advantages, it is undeniable that their convergence on principles of precision, efficiency, and minimal environmental impact is significant.
As we face the challenges and opportunities of the future, it is crucial to recognize that sustainable manufacturing is not a destination but an ongoing journey. It requires the harmonious interplay of technological innovation, regulatory support, research collaboration, and social awareness. The legacy we leave for future generations depends on the choices we make today. By integrating sustainability into every aspect of manufacturing, we can weave a tapestry of progress, prosperity, and a greener tomorrow.
Comment