In the ever-evolving manufacturing industry, the integration of Artificial Intelligence (AI) and Machine Learning (ML) with metal stamping processes is ushering in a new era of efficiency, precision, and innovation. This powerful synergy is transforming an ancient technique into a cutting-edge field where complex designs, impeccable quality, and optimized production converge. In this article, we will delve into how AI and ML are revolutionizing metal stamping technology and pushing it to the forefront of modern manufacturing.
Enhanced Design and Simulation
AI and ML algorithms are making significant strides in the metal stamping sector by greatly enhancing the capabilities of the design and simulation phase. Take, for example, a company specializing in the production of automotive components. Traditionally, designing complex stamping dies required iterative cycles and expert input. Now, this company utilizes AI and ML to input historical design data, material properties, and performance metrics into algorithms. The optimized die designs generated by these algorithms not only ensure accuracy but also minimize material waste and streamline the production process.
Advertisement
Furthermore, simulations supported by AI and ML can comprehensively understand the impact of various variables on the stamping outcome. Engineers can virtually test a range of scenarios from altering material thickness to adjusting stamping pressure. These simulations allow for rapid experimentation without the need for physical prototypes, thus accelerating the design process and contributing to the creation of more efficient and reliable stamping processes.
Predictive Maintenance of Stamping Presses (Stamping Machines)
Imagine a large metal stamping factory responsible for producing casings for consumer electronics. The factory operates around the clock, and any unexpected downtime can result in significant losses. The intervention of AI and ML can mitigate this challenge. By continuously analyzing data generated by sensors embedded in the stamping machines, these technologies can predict when components may fail. This allows for scheduled preventive maintenance, avoiding costly breakdowns and maintaining seamless production.
For instance, sensors can monitor factors such as vibration levels, temperature fluctuations, and hydraulic pressures. AI algorithms analyze this data in real-time and detect patterns that precede mechanical failures. If a potential issue is identified, the maintenance team receives an automatic alert, enabling them to address the problem before it escalates. As a result, unplanned downtime is minimized, and the reliability and efficiency of equipment operation are enhanced.Optimizing Mold Design
An aerospace component manufacturer faces the complex task of designing molds for intricate precision parts. Traditional methods require time-consuming adjustments and testing. Artificial intelligence (AI) and machine learning (ML) have transformed this process. By processing a vast array of design parameters, material properties, and production variables, these technologies can rapidly generate mold designs that ensure accuracy and durability. This accelerated design phase allows aerospace manufacturers to meet stringent quality standards while reducing production cycles.
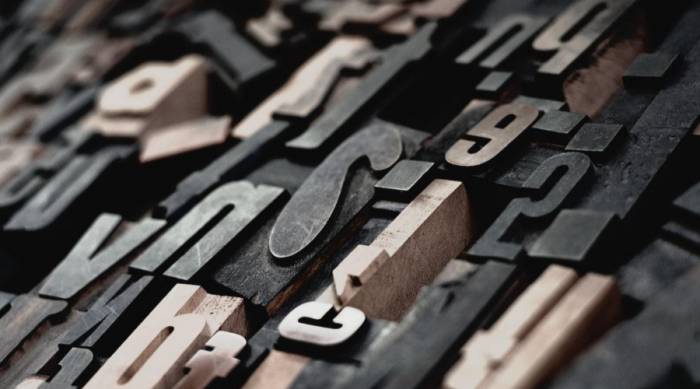
Moreover, AI-driven simulations play a crucial role in optimizing tooling and mold design. Engineers can simulate the entire stamping process, analyzing the impact of different mold geometries, materials, and processing conditions on the final product. By virtually fine-tuning these variables, manufacturers can determine the optimal settings for maximizing efficiency and minimizing defects. This data-driven approach to mold design helps improve part quality and reduce manufacturing costs.
Real-Time Quality Control
In the production of precision medical equipment through metal stamping operations, consistent quality is of utmost importance. Even minor defects can have severe consequences. AI and ML are used to monitor each stamping cycle in real-time. By analyzing sensor data and historical performance, these technologies can detect deviations that may indicate the presence of defects in the parts. Once an anomaly is detected, the system halts production and alerts the operator, ensuring that only flawless parts proceed to the assembly line.
For instance, sensors can measure variables such as stamping force, material thickness, and product dimensions. AI algorithms compare real-time data with established quality thresholds, and any deviations are immediately flagged. This level of real-time quality control not only reduces the risk of defective products reaching consumers but also minimizes the need for post-production inspections, saving time and resources.
Reducing Material Waste
To reduce waste and environmental impact, a sustainable manufacturing plant has adopted AI and ML-driven material optimization strategies. By analyzing the geometry of stamped parts and considering factors such as material characteristics and production constraints, these technologies determine the most efficient arrangement for each stamping run. This meticulous optimization minimizes material waste, saving significant costs and aligning with the plant's commitment to environmental conservation.Suppose a certain factory produces complex metal components for electronic devices. Through artificial intelligence-driven simulations, engineers have determined the optimal nesting pattern for stamping these components onto metal sheets. By minimizing the gaps between parts and making full use of available space, the factory has significantly reduced material waste. This not only helps to save costs but also reduces the environmental impact of the manufacturing process.
Adaptive Process Optimization
The environmental conditions in metalworking workshops vary and can affect the stamping outcomes. Artificial intelligence and machine learning (ML) algorithms continuously monitor these conditions and adjust stamping parameters in real-time. For instance, during hot and humid weather, the algorithm might suggest slight adjustments to the stamping pressure and speed. Regardless of how external factors change, this adaptability ensures consistent product quality, ultimately improving customer satisfaction and reducing rework.
In high-precision metal stamping operations, variations in temperature and humidity can affect the behavior of the material and the performance of the stamping machine. AI algorithms analyze real-time sensor data and historical performance records to detect correlations between environmental conditions and stamping outcomes. Based on these insights, the algorithms dynamically adjust the stamping process to ensure that each part meets the required specifications. This adaptability enhances product quality and reduces the likelihood of defects caused by environmental fluctuations.
Optimizing the Supply Chain
The supply chain of multinational automotive manufacturers is intricate. Artificial intelligence and ML are used to predict demand fluctuations, anticipate disruptions caused by geopolitical events or natural disasters, and optimize procurement decisions. These technologies inform the manufacturer's supply chain strategy by analyzing historical data, market trends, and even news information. As a result, companies can maintain supply chain resilience, minimize production interruptions, and ensure timely deliveries.
For example, during periods when geopolitical tensions might affect the supply of key raw materials, AI algorithms analyze historical supply chain data to identify alternative sourcing options. These algorithms consider factors such as transportation costs, delivery times, and supplier reliability to recommend the most suitable alternatives. By proactively adopting a diversified sourcing strategy, manufacturers reduce their vulnerability to supply chain disruptions and ensure a stable material flow for metal stamping operations.Faster Time to Market
A consumer electronics company is gearing up to launch a groundbreaking product, but time is of the essence. Artificial Intelligence (AI) and Machine Learning (ML) have accelerated the progress of the prototype design phase. Virtual simulations driven by these technologies can accurately predict the performance of stamping components under various conditions. This allows engineers to fine-tune the design virtually, reducing the need for physical prototypes and costly iterations. What's the result? A significantly shortened development cycle and an enhanced competitive edge in the market.
Suppose a company is developing a new smartphone that requires complex metal parts. By leveraging AI-driven simulations, engineers can virtually test different stamping parameters, material selections, and product designs. Through this virtual experimentation, they can determine the optimal configuration that meets performance requirements and production constraints. Consequently, the company can rapidly iterate design concepts, make informed decisions, and expedite the product development timeline.
Continuous Learning and Improvement
The true allure of AI and ML lies in their ability to learn continuously. In custom metalworking enterprises, these technologies are used to monitor the performance of newly developed stamping processes. Over time, as data accumulates, the algorithms learn from each cycle, identifying subtle patterns and refining their recommendations. This iterative learning process improves process efficiency, reduces defects, and ultimately enhances customer satisfaction.
Consider an aerospace manufacturer specializing in lightweight stamped components for aircraft. AI algorithms continuously analyze data from stamping operations, identifying correlations between process parameters and product quality. As the algorithms accumulate more data, they become increasingly adept at predicting the best stamping conditions for different materials and geometries. This ongoing learning process not only improves product consistency but also helps develop best practices, propelling the entire industry forward.
In summary, integrating AI and ML into metal stamping processes is driving a revolution in manufacturing. From enhancing design and predictive maintenance to real-time quality control and supply chain optimization, these technologies are reshaping the methods and execution of metal stamping. As AI and ML technologies continue to advance, the potential for further innovation in the field of metal stamping is limitless, promising a future of precision, efficiency, and excellence.
Comment