In the rapidly evolving field of mold engineering, precision, efficiency, and adaptability are of paramount importance. A wave of innovation has surged forth, completely transforming the way we design, manufacture, and optimize molds. Utilizing cutting-edge technologies and novel methods, engineers and manufacturers are continually pushing the boundaries of mold engineering. In this comprehensive article, we will delve into the outstanding advancements reshaping the industry, propelling it towards a future of enhanced performance, reduced costs, and sustainable development.
CAD/CAE Technology: Pioneering Precision and Efficiency
At the heart of modern mold engineering is the integration of Computer-Aided Design (CAD) and Computer-Aided Engineering (CAE) software. These technological marvels enable designers and engineers to create, analyze, and optimize molds with unparalleled precision. Through complex simulations and modeling, CAD/CAE technology offers a window into predicting mold performance, thereby significantly shortening the design cycle and minimizing costs. The perfect fusion of digital ingenuity and engineering acumen ensures that molds are not only conceptualized but also meticulously refined into perfect products, leading to the production of exceptional, durable goods.
Advertisement
Revolutionizing Rapid Prototyping with 3D Printing Technology
In the era of rapid innovation, traditional prototyping methods have given way to extraordinary advancements: three-dimensional printing. This revolutionary technology can quickly create complex mold prototypes, accelerate the verification process, and significantly reduce development time. The combination of rapid prototyping and mold engineering has opened up a realm of infinite possibilities, allowing engineers to refine designs with unprecedented speed and accuracy. As 3D printing technology continues to evolve, the application scope of mold engineering technology is also expanding, reshaping the landscape across various industries and driving their progress.
The Rise of Smart Molds: Sensors and Real-Time Monitoring
By integrating sensors, data acquisition, and remote monitoring technologies, mold engineering has entered the smart era. Real-time insights into mold conditions enable manufacturers to monitor and analyze mold performance, optimize production efficiency, and prevent potential failures. The ability to remotely monitor molds not only enhances productivity but also paves the way for proactive maintenance, minimizing downtime and improving operational continuity. The emergence of smart molds heralds a new era of manufacturing processes that are efficient and reliable.Structural Optimization: The Perfect Fusion of Form and Function
In pursuit of efficiency and sustainable development, mold engineers are employing advanced technologies such as simulation-driven optimization and morphological analysis. These methods allow for fine-tuning of mold structures, enhancing overall performance while reducing material consumption. Mold engineering is no longer confined to traditional design; it is a field where innovation and structural optimization merge, enabling the creation of stylish, robust, and tailor-made perfect molds.
Precision Manufacturing: Elevating the Level of Craftsmanship
Nowadays, mold engineering technology is closely linked with precision manufacturing techniques such as ultra-precision machining. This synergy ensures that the production of molds achieves unparalleled precision, resulting in smoother and more delicate mold surfaces. Precision manufacturing not only enhances the aesthetic appeal of molds but also strengthens their functionality, ensuring that molds perform at their best and contribute to the production of flawless final products.
Adaptive Control: Mastering Variability
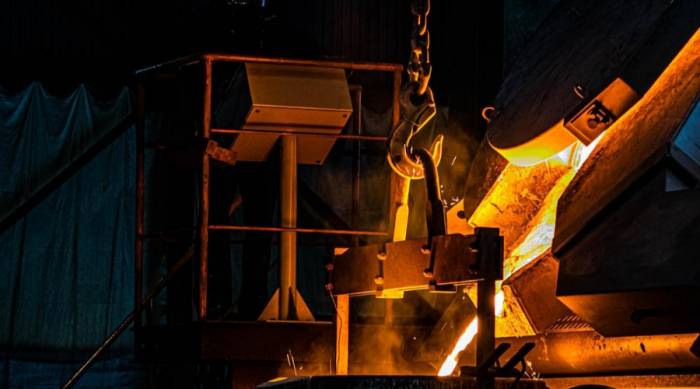
In the dynamic environment of the manufacturing industry, molds must adapt to various operating conditions. Adaptive control technology uses algorithms to autonomously adjust mold parameters in response to changing environments. This innovation improves production stability, consistency, and product quality, laying the foundation for seamless operation in different production environments.Virtual Reality and Augmented Reality: Building a Bridge to a Better Mold
Virtual Reality (VR) and Augmented Reality (AR) technologies are not just limited to entertainment; they are transforming mold engineering. Through VR and AR simulations, engineers can visually see mold assembly, simulate maintenance procedures, and facilitate operator training. This immersive approach can reduce errors, accelerate the learning curve, and improve overall production efficiency, thus establishing a new paradigm for mold design and operation.
Leveraging Artificial Intelligence and Machine Learning: A New Frontier
In the age of data, mold engineering is undergoing a transformative journey driven by Artificial Intelligence (AI) and Machine Learning (ML). These technologies can analyze vast amounts of performance data, providing insights that drive improvements in mold design and production optimization. The integration of AI and ML not only enhances the lifespan and stability of molds but also promotes the tailoring of molds according to the unique demands of each production cycle.
Self-Healing Materials: Extending Mold Lifespan
Imagine molds that can heal themselves—this concept is rapidly becoming a reality through the development of self-healing materials. These cutting-edge substances possess the remarkable ability to autonomously repair damage, extending the lifespan of molds and significantly reducing maintenance requirements. The integration of self-healing materials is expected to prolong mold life, minimize operational interruptions, and enhance productivity and efficiency.
Nano Coating Technology: Enhancing Mold Performance
Nano coating technology is revolutionizing mold performance by providing advanced surface treatments that increase durability, reduce wear, and improve resistance to various environmental factors. These coatings can also facilitate easier release of the molded parts, leading to reduced production times and improved part quality. The application of nano coatings is a significant step forward in enhancing the performance and longevity of molds in various industries.Nanotechnology is making a significant impact in the field of mold engineering, with its use of nanoscale materials and coatings significantly enhancing mold performance. These nano-enhanced elements improve the wear resistance, corrosion resistance, and heat resistance of molds, thereby enhancing the overall performance and durability of the molds. As nanotechnology continues to mature, it is poised to become the cornerstone of mold engineering, bringing revolutionary changes to various industries and paving the way for unparalleled product quality.
Flexible mold adjustment: Meeting diverse production needs
The characteristic of the manufacturing industry is constant change, and mold engineering is no exception. The emergence of agile mold adjustment technology has changed the game, allowing for the rapid reconfiguration of molds to accommodate different product sizes. This innovation optimizes production flexibility, reduces changeover times, and ensures that manufacturers can quickly adapt to the ever-changing market demands.
Green manufacturing: Molds for a sustainable future
As environmental issues become a focal point of concern, mold engineering is also adopting the principles of green manufacturing. Engineers are exploring eco-friendly materials and production methods to minimize the environmental impact of the mold manufacturing process. By adopting sustainable practices, mold engineers are pioneering a new era of responsible manufacturing where efficiency and environmental management coexist harmoniously.
Comprehensive mold data management: Maximizing lifecycle
The lifecycle of a mold extends far beyond the initial manufacturing phase. To ensure optimal performance and longevity, comprehensive mold data management systems are being established. These systems meticulously record information on mold design, manufacturing, usage, and maintenance, providing a holistic view of the mold's lifecycle. Insights gained from data-driven analysis enable manufacturers to refine mold designs, optimize production processes, and extend the lifecycle of molds.Advanced Cooling Technology: Enhancing Efficiency
Efficient cooling is the cornerstone of successful mold engineering, and innovation is transforming the face of cooling technology. Ingenious cooling solutions continue to emerge, improving mold cooling efficiency, reducing processing times, and enhancing overall production efficiency. As mold cooling technologies continue to evolve, they are reshaping the industry landscape, accelerating the manufacture of higher quality products.
Mold Manufacturing Flexibility: Adapting to Change
In an era of diverse consumer demands, mold engineering considers flexibility as a virtue. Flexible mold manufacturing technologies are becoming a solution that allows manufacturers to quickly switch between products of different shapes and sizes. This adaptability minimizes downtime, reduces costs, and ensures that manufacturers can seamlessly respond to the ever-changing market dynamics.
Bio-inspired Engineering: Taking Nature as a Blueprint
Nature has always been a source of inspiration for innovation, and mold engineering is no exception. Engineers draw inspiration from biological structures and mechanisms, integrating biomimicry techniques into mold design. This approach leverages the elegance and efficiency of nature's own engineering marvels, making molds more resilient, efficient, and durable.Multi-Material Stamping: Breaking Boundaries
Sophisticated product designs demand innovative solutions. Multi-material stamping technology is a testament to the evolution of die engineering, enabling the combination and layering of various materials to create complex parts with enhanced performance and functionality. This groundbreaking approach has propelled the creation of products that not only possess visual impact but also transcend the limits achievable by die engineering.
In summary, driven by cutting-edge technology and innovative methods, the field of die engineering is undergoing a profound transformation. From precise CAD/CAE design to adaptive control algorithms, from self-healing materials to flexible die adjustments, each innovation outlined in this review attests to the indomitable spirit of human creativity. Die engineering is no longer confined to traditional patterns; it is a field brimming with infinite possibilities where performance, efficiency, and sustainability converge to shape a future defined by excellence.
Comment